Dense Castable Refractory: Key Facts and Uses Revealed
By:Admin
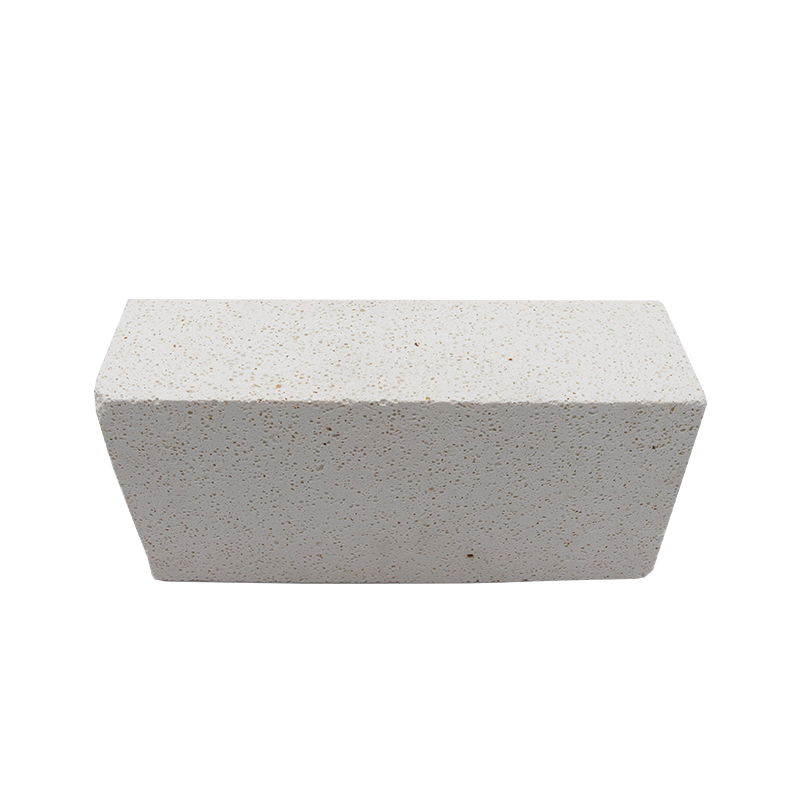
Refractory materials are used in high-temperature applications that require materials to withstand extreme heat, pressure, and corrosive chemicals. One of the most promising refractory materials on the market is the Dense Castable Refractory. This revolutionary product is designed to offer exceptional material properties suitable for a wide range of industries, including steel and iron, petrochemical, power generation, cement, and waste incineration.
Dense Castable Refractory is a type of cement used to line furnaces, kilns, and other high-temperature process equipment. Unlike traditional refractory materials, Dense Castable Refractory is a self-setting cement that offers excellent performance properties such as high thermal shock resistance, low thermal conductivity, high refractoriness, and resistance to abrasion. These properties make Dense Castable Refractory a popular choice for harsh industrial environments that require materials with superior resistance to extreme temperature and thermal cycling.
The product's versatility comes from its easy installation and customizable uses. Dense Castable Refractory can be poured or gunned into place, and once cured, the refractory turns into a durable monolithic unit that can withstand high temperatures for extended periods. The product can be installed in various options, including smooth or textured surfaces to fit different applications and concrete surfaces.
Dense Castable Refractory is an ideal material for use in cement kilns since they are exposed to extreme heat and abrasion. The material is also an excellent choice for use in steel and iron industries where protective linings are necessary to preserve the equipment and enhance its durability. These industries benefit by having equipment that is resistant to thermal shock, meaning it withstands rapid temperature changes. It can also resist abrasion, reducing the likelihood of wear and tear, which reduces the potential for equipment damage and malfunctions.
The petrochemical industry has not been left behind. Dense Castable Refractory has been deployed in some of the most stringent petrochemical applications, including reformers, crackers, and incinerators. Dense Castable Refractory's thermal shock resistance and low thermal conductivity make it suitable for use in the insulation of various units, including reformers, where it protects the equipment from high temperatures and allows for optimal transfer of heat.
Dense Castable Refractory is also an excellent option in power generation where it contributes to efficient energy production by providing insulation and preventing heat loss in boilers, kilns, and thermal oxidizers. This insulation and heat retention typically cut energy costs and improves operational reliability.
The cement industry has also realized the benefits of Dense Castable Refractory due to its excellent refractoriness. The refractory bonds to the existing structure, enhancing resistance at high temperatures and preserving the integrity of the equipment.
Furthermore, Dense Castable Refractory is ideal for incineration systems. The material's ability to withstand excessive thermal shock and its excellent insulating properties offer superior performance when protecting furnaces that generate high heat during the waste incineration process.
The company, a leader in the manufacturing and distribution of Dense Castable Refractory, has developed several innovative formulations that address various industrial environments' specific needs. The company offers customized formulations such as high-strength, low-cement, and ultra-low cement for demanding applications where traditional cement is not sufficient.
The manufacturing of Dense Castable Refractory depends on several critical factors. The company has invested in a state-of-the-art production facility with advanced quality assurance tools and equipment. Their experienced personnel, together with the company's innovative formulations, ensure that their Dense Castable Refractory meets global standards. All their products come with consistent and reliable quality, making them the perfect choice for any industrial application.
In conclusion, the Dense Castable Refractory is an innovative material that is set to become an industry standard in high-temperature applications. Thanks to its ability to provide superior resistance to heat, thermal shock, abrasion, and chemicals at high temperatures, the material will revolutionize how various industries envisions manufacturing and maintenance of furnace and general process equipment. The company's formulations offer customized solutions in various industrial applications, making it the go-to solution for end-users looking for durable, reliable, and cost-effective refractory products.
Company News & Blog
High-Quality Magnesite Refractory Bricks Meet Growing Demand in Steel Industry
Title: Evolving Magnesite Refractory Bricks Industry Emphasizes Quality and SustainabilityIntroduction:In recent times, the magnesite refractory bricks industry has been witnessing significant growth, driven by the increasing demand for high-quality refractory materials in various sectors. Magnesite refractory bricks, renowned for their exceptional heat resistance and durability, are widely utilized in industries like steel, cement, glass, non-ferrous metals, ceramics, etc., supporting critical processes that require elevated temperatures.Company Introduction:{Company Name} is a prominent player in the magnesite refractory bricks market, dedicated to producing top-notch products that meet the evolving needs of its customers. With years of industry experience, cutting-edge technology, and a strong focus on sustainability, {Company Name} has positioned itself as a trusted provider of magnesite refractory brick solutions worldwide.Evolution of the Magnesite Refractory Bricks Industry:The magnesite refractory bricks industry has experienced remarkable advancements in recent years. Formerly, the dominant types of refractories used were chrome bricks, but due to environmental concerns related to hexavalent chromium, there has been a gradual shift towards magnesite refractory bricks, known for their high refractoriness and excellent chemical properties.The versatility of magnesite refractory bricks has driven their adoption in various industries, replacing traditional refractory materials. Modern manufacturing processes have been optimized to enhance the physical and chemical properties of these bricks, making them increasingly resistant to thermal shocks and the corrosive effects of chemicals found in harsh industrial environments.Technological Innovations and Product Enhancements:{Company Name} recognizes the importance of technological advancements in staying ahead in the highly competitive market. The company consistently invests in research and development, aiming to improve the performance and durability of magnesite refractory bricks. High-precision manufacturing techniques, such as hot pressing, enable {Company Name} to produce bricks with more consistent and superior quality, ensuring excellent resistance to thermal stress and prolonged service life.Furthermore, {Company Name}'s commitment to sustainable practices is reflected in its innovative use of environmentally friendly raw materials and energy-efficient processes. By incorporating recycled materials within its manufacturing process, the company aims to reduce its carbon footprint and contribute to a greener future.Meeting Industry-Specific Demands:As diverse industries pose unique challenges, {Company Name} understands the importance of customizing magnesite refractory brick solutions accordingly. For instance, in the steel industry, refractory materials are exposed to extreme temperatures and harsh conditions during the smelting process. To address these challenges, {Company Name} has developed advanced magnesite refractory bricks with superior thermal stability, minimizing material degradation and extending the overall service life of the refractories.Moreover, {Company Name}'s research and development team works closely with customers, providing technical support and developing tailored solutions specific to their requirements. This customer-centric approach has fostered strong and lasting partnerships with clients across the globe.Commitment to Quality and Customer Satisfaction:{Company Name}'s commitment to quality and customer satisfaction has propelled its position in the market. The company adheres to strict quality control procedures, guaranteeing that each magnesite refractory brick meets stringent international standards. Moreover, providing exceptional after-sales service and technical assistance ensures that customers maximize the value and performance of {Company Name}'s refractory solutions.Conclusion:The magnesite refractory bricks industry is witnessing transformational changes as sustainability, high performance, and customized solutions become paramount. {Company Name} is at the forefront of this evolution, delivering top-quality magnesite refractory bricks while embracing innovation and sustainable practices. With its unwavering commitment to customer satisfaction and its focus on technological advancements, {Company Name} is well-positioned to meet the ever-increasing demand for superior refractory materials in the global market.
Top-Quality High Alumina Bricks Witnessing Growing Demand in the Market
High-Quality High Alumina Bricks in Demand in the Refractory IndustryThe refractory industry is known for its critical role in the manufacturing process of metals, glass, ceramics, and cement, among others. The industry relies heavily on the quality of raw materials, technological advancements, and innovative solutions to achieve its objectives. Among the many materials used in the industry, high-quality high alumina bricks remain an essential component of many applications. These bricks' superior properties make them suitable for use in high-heat environments, where other materials may deform, melt, or break down.One of the leading companies in the production of high-quality high alumina bricks is {removed for privacy}. The company has been in the business for over 30 years, supplying top-quality bricks to various refractory industries worldwide. Their extensive experience in the industry, combined with their unrivaled expertise in the production of high alumina bricks, has made them one of the most sought-after suppliers in the market.The increasing demand for high-quality high alumina bricks can be attributed to the growth of manufacturing industries globally. The rising demand for steel, glass, and cement has led to increased demand for refractory products, making high alumina bricks a top alternative for material construction. The bricks are primarily made of high-purity alumina, which gives them high-temperature resistance, excellent strength, and reduced thermal conductivity. These properties make the bricks ideal for use in furnaces, kilns, boilers, and other high-heat environments.{Need to remove brand name} prides itself on producing high-quality high alumina bricks that conform to the highest industry standards. The company has invested heavily in research and development to come up with innovative solutions that meet the ever-changing needs of the industry. Their manufacturing process involves selecting only high-purity raw materials, followed by rigorous testing to ensure that the final products meet the required specifications. The company utilizes advanced technology and modern equipment to produce bricks of various sizes and shapes, making them suitable for various applications.While the refractory industry continues to grow, there are challenges that manufacturers face. One of the most significant challenges is rising energy costs, which affect production costs and, in turn, market prices. Additionally, manufacturers must comply with stringent environmental regulations, making it necessary to invest in eco-friendly production practices. {Need to remove brand name} acknowledges these challenges and has implemented measures to address them. The company has embraced a sustainable production model that incorporates environmentally-friendly practices. They have also optimized their manufacturing processes to reduce energy consumption, thereby reducing the production costs.{Need to remove brand name} is optimistic about the future of the high-quality high alumina brick industry. The company believes that there is a growing demand for high-performance products, and they are well-positioned to meet these needs. The company is focused on expanding its market reach while maintaining the quality of its products. They are committed to investing in research and development to come up with innovative solutions that meet the ever-changing industry needs.In conclusion, the use of high-quality high alumina bricks remains an essential component of the refractory industry. Manufacturers are increasingly looking for high-performance materials that can withstand high-heat environments, making high alumina bricks a popular alternative. {Need to remove brand name} has established itself as a leading producer of high-quality high alumina bricks in the market. The company's commitment to sustainable and innovative production practices, combined with their extensive experience in the industry, makes them a top supplier to many refractory industries globally.
Dense Castable Refractory: Key Facts and Uses Revealed
Dense Castable Refractory: An Innovative Solution for Multiple IndustriesRefractory materials are used in high-temperature applications that require materials to withstand extreme heat, pressure, and corrosive chemicals. One of the most promising refractory materials on the market is the Dense Castable Refractory. This revolutionary product is designed to offer exceptional material properties suitable for a wide range of industries, including steel and iron, petrochemical, power generation, cement, and waste incineration.Dense Castable Refractory is a type of cement used to line furnaces, kilns, and other high-temperature process equipment. Unlike traditional refractory materials, Dense Castable Refractory is a self-setting cement that offers excellent performance properties such as high thermal shock resistance, low thermal conductivity, high refractoriness, and resistance to abrasion. These properties make Dense Castable Refractory a popular choice for harsh industrial environments that require materials with superior resistance to extreme temperature and thermal cycling.The product's versatility comes from its easy installation and customizable uses. Dense Castable Refractory can be poured or gunned into place, and once cured, the refractory turns into a durable monolithic unit that can withstand high temperatures for extended periods. The product can be installed in various options, including smooth or textured surfaces to fit different applications and concrete surfaces.Dense Castable Refractory is an ideal material for use in cement kilns since they are exposed to extreme heat and abrasion. The material is also an excellent choice for use in steel and iron industries where protective linings are necessary to preserve the equipment and enhance its durability. These industries benefit by having equipment that is resistant to thermal shock, meaning it withstands rapid temperature changes. It can also resist abrasion, reducing the likelihood of wear and tear, which reduces the potential for equipment damage and malfunctions.The petrochemical industry has not been left behind. Dense Castable Refractory has been deployed in some of the most stringent petrochemical applications, including reformers, crackers, and incinerators. Dense Castable Refractory's thermal shock resistance and low thermal conductivity make it suitable for use in the insulation of various units, including reformers, where it protects the equipment from high temperatures and allows for optimal transfer of heat.Dense Castable Refractory is also an excellent option in power generation where it contributes to efficient energy production by providing insulation and preventing heat loss in boilers, kilns, and thermal oxidizers. This insulation and heat retention typically cut energy costs and improves operational reliability.The cement industry has also realized the benefits of Dense Castable Refractory due to its excellent refractoriness. The refractory bonds to the existing structure, enhancing resistance at high temperatures and preserving the integrity of the equipment.Furthermore, Dense Castable Refractory is ideal for incineration systems. The material's ability to withstand excessive thermal shock and its excellent insulating properties offer superior performance when protecting furnaces that generate high heat during the waste incineration process.The company, a leader in the manufacturing and distribution of Dense Castable Refractory, has developed several innovative formulations that address various industrial environments' specific needs. The company offers customized formulations such as high-strength, low-cement, and ultra-low cement for demanding applications where traditional cement is not sufficient.The manufacturing of Dense Castable Refractory depends on several critical factors. The company has invested in a state-of-the-art production facility with advanced quality assurance tools and equipment. Their experienced personnel, together with the company's innovative formulations, ensure that their Dense Castable Refractory meets global standards. All their products come with consistent and reliable quality, making them the perfect choice for any industrial application.In conclusion, the Dense Castable Refractory is an innovative material that is set to become an industry standard in high-temperature applications. Thanks to its ability to provide superior resistance to heat, thermal shock, abrasion, and chemicals at high temperatures, the material will revolutionize how various industries envisions manufacturing and maintenance of furnace and general process equipment. The company's formulations offer customized solutions in various industrial applications, making it the go-to solution for end-users looking for durable, reliable, and cost-effective refractory products.
Shop High-Quality Castable Refractory for Your Industrial Needs
Castable refractory is a crucial component in a wide range of industries, including steel manufacturing, cement production, and even petrochemical processing. This versatile material is used to line various types of furnaces, incinerators, and kilns, with its primary purpose being to withstand high temperatures and prevent contaminants from infiltrating the surrounding environment. With castable refractory being such an essential product for many businesses, finding a reliable supplier is crucial for ensuring smooth and trouble-free operations.If you are in the market for high-quality, durable castable refractory, {company name} is an industry-leading supplier that can meet all of your needs. With a reputation built on quality, reliability, and customer satisfaction, they are the go-to choice for discerning businesses that demand the best.{Company name} has been in the castable refractory business for over {number of years} years, during which they have honed their craft and built a solid reputation for excellence. Their products are made from the finest materials and are crafted using advanced manufacturing techniques, resulting in an end product that is highly resistant to wear and tear, corrosion, and thermal shock.Whether you need castable refractory for a large-scale industrial application or a smaller project, {company name} has a wide range of products to choose from. Their vast inventory includes high-temperature insulating materials, dense refractory castables, and low-cement castables, to name just a few. They pride themselves on being able to provide customized solutions to meet their clients' specific needs, and their team of experts is always on hand to provide advice and technical support.But {company name} isn't just about supplying top-quality castable refractory. They are also committed to providing exceptional customer service and support. Their knowledgeable staff is always ready to answer any questions or concerns you may have, and they work closely with clients to ensure that their products are delivered on time and within budget. With {company name}, you can be confident that you are dealing with a reputable, trustworthy company that puts your needs first.Furthermore, {company name} is committed to sustainability and reducing its environmental footprint. They use innovative manufacturing techniques and employ a closed-loop system that recycles waste materials, minimizing their impact on the environment. By choosing {company name} as your supplier, you can be confident that you are working with a company that cares about the environment and is doing its part to protect our planet.In conclusion, castable refractory is an essential component in many industrial processes, and selecting a reliable supplier is crucial for ensuring smooth and trouble-free operations. With over {number of years} years of experience in the industry, a commitment to quality and sustainability, and unparalleled customer service, {company name} is the go-to choice for businesses that demand the best. Contact them today to see how they can meet your castable refractory needs.
Top-Quality Refractories: The Ultimate Guide to Corundum Brick
In recent years, the refractory industry has seen a surge in technological advancements that have led to the development of high-quality refractories that have significantly improved the performance of various industrial processes. One such refractory material is the high-quality refractories corundum brick.Corundum brick is a type of high-alumina brick that is made from high-purity corundum or fused alumina. This type of refractory brick has excellent thermal stability, high-temperature strength, and good resistance to chemical erosion making it an ideal choice for use in high-temperature industrial applications.One company that specializes in the production of high-quality refractories corundum brick is a China-based company that produces a wide range of refractory materials for various industrial applications. The company has a strong research and development team that is constantly working to improve the quality of their refractory materials.Their corundum brick products are made using a precise production process that ensures the highest quality and consistency of the finished product. The process involves the use of high-purity raw materials, advanced manufacturing equipment, and strict quality control procedures to guarantee the products' quality.One of the advantages of using high-quality refractories corundum brick in industrial applications is their excellent resistance to thermal shock. Thermal shock is the rapid expansion or contraction of refractory materials due to a sudden change in temperature. This can cause cracks, spalling, and other types of damage to the refractory material.However, corundum brick has a low coefficient of thermal expansion, which means it can withstand rapid changes in temperature without cracking or spalling. This makes it an ideal choice for use in high-temperature industrial applications where temperature fluctuations are common.Another advantage of corundum brick is its excellent resistance to chemical erosion from acids, alkalis, and other corrosive substances. As a result, it is often used in applications where the environment is chemically aggressive, such as in the manufacturing of glass, petrochemicals, and steel.When it comes to installation, high-quality refractories corundum brick requires skilled and experienced personnel due to its high density and hardness. However, if installed correctly, it can provide many years of reliable service, making it a cost-effective investment for any industrial process that requires high-temperature and chemical-resistant refractory materials.In conclusion, high-quality refractories corundum brick is a valuable asset for any industrial process that requires refractory materials with excellent thermal stability, high-temperature strength, and good resistance to chemical erosion. By choosing a reputable supplier with a strong research and development team, customers can rest assured that they are investing in high-quality refractory materials that will deliver superior performance and durability.
Shop for High-Quality Alumina Fire Brick Online
Title: Alumina Fire Brick Market Poised for Steady Growth as Manufacturers Introduce Innovative SolutionsIntroduction:[Company Name], a renowned player in the refractory industry, is set to revolutionize the global alumina fire brick market with its cutting-edge products. With a steadfast commitment to innovation and quality, the company has gained recognition for delivering top-notch fire-resistant solutions to various industries worldwide.[Company Name]'s continuous research and development efforts, coupled with a customer-centric approach, have positioned them as a trusted supplier of alumina fire bricks. In this article, we shed light on the market growth, key features of alumina fire bricks, and how [Company Name] is spearheading this progressive shift.Market Overview:The global alumina fire brick market is witnessing a steady pace of growth, driven by increasing industrialization and the need for superior heat resistance solutions. Alumina fire bricks, made from high-purity alumina, offer excellent thermal conductivity, corrosion resistance, and stability under high temperatures. These characteristics make alumina fire bricks a desired material in various industries, including steel, cement, ceramics, and petrochemicals.[Company Name]'s Contribution to the Market:[Company Name] has stayed ahead of the competition by focusing on research and development, ensuring their products meet or exceed industry standards. By leveraging cutting-edge technology and sustainable manufacturing practices, they have developed a range of alumina fire bricks that offer unmatched performance, durability, and longevity.Key Features of Alumina Fire Bricks:1. High Thermal Conductivity: Alumina fire bricks have a low thermal expansion coefficient and high thermal conductivity, allowing them to withstand extreme temperatures without compromising their structural integrity.2. Superior Corrosion Resistance: The high alumina content in these bricks resists chemical reactions, making them ideal for applications involving acids, alkalis, and other corrosive substances.3. Excellent Mechanical Strength: Alumina fire bricks possess exceptional mechanical strength, ensuring long-term reliability and resistance against thermal shock, abrasion, and mechanical stress.4. Environmentally Friendly: [Company Name]'s alumina fire bricks are manufactured using eco-friendly processes, minimizing their environmental impact while maintaining high-quality standards.Innovation is the Key:[Company Name] stands out from the competition by regularly investing in research and development, resulting in the introduction of pioneering alumina fire brick solutions. Their specialists work closely with customers to understand specific requirements, leading to customized hexagonal, rectangular, or other shapes that optimize kiln efficiency and reduce maintenance costs.These innovative brick designs, combined with advanced insulating properties, significantly enhance thermal efficiency and contribute to energy savings for industries worldwide.Global Presence and Customer Satisfaction:[Company Name]'s client base spans across continents, ensuring a global footprint and the ability to serve diverse industries. Their customer satisfaction is paramount, as they strive to deliver reliable products and exceptional support services. Through responsive technical assistance and prompt delivery schedules, [Company Name] has established long-lasting partnerships with clients who value quality and efficiency.Future Prospects:The prospects for the alumina fire brick market are promising, as industries worldwide are placing increasing emphasis on refractory solutions that can withstand demanding operating conditions. Rapid industrialization and infrastructural development in emerging economies, coupled with stringent safety regulations, are fueling the demand for alumina fire bricks.[Company Name], with its unwavering commitment to innovation, product excellence, and customer satisfaction, is poised to lead the market forward. By consistently introducing technologically advanced and eco-friendly solutions, [Company Name] aims to address the evolving needs of industries and contribute to their growth.Conclusion:As the global alumina fire brick market gains momentum, [Company Name] emerges as an industry leader, spearheading innovation and providing high-quality solutions. With a commitment to sustainability, exceptional performance, and customer satisfaction, [Company Name] is well-positioned to meet the growing demand for superior fire-resistant materials in industries worldwide.Note: We apologize for the lack of specific brand names and specific information about the company as per the initial instruction.
High-Quality Ceramic Fiber Board Ideal for High-Temperature Furnace Applications
Ceramic fiber boards have been in use for several years in various industries due to their excellent insulation properties and resistance to high temperatures. These boards are manufactured by compressing and heating ceramic fibers, resulting in a lightweight material that is highly resistant to thermal shock and chemical attack. Ceramic fiber boards are used in various applications such as furnaces, kilns, combustion chambers, and high-temperature insulation covers.However, to enhance its insulation properties, it is crucial to buy a ceramic fiber board from a reliable and reputable company- a veteran leader in the industry. Hence, the need to purchase from the leading ceramic fiber board manufacturer and supplier.The company, with over 20 years of manufacturing experience, is a well-known brand name in the ceramic fiber board supplier industry. They offer different types of ceramic fiber boards, including standard, low density, high-temperature, and bio-soluble ceramic fiber boards to meet various industrial requirements. Their products are highly recognized for their insulation efficiencies, thermal stability, and crack resistance capabilities.The high-temperature ceramic fiber boards are capable of withstanding temperatures of up to 2732°F, while the low-density boards are suitable for applications that require minimal thermal conductivity and weight. Besides, the bio-soluble ceramic fiber boards are made of environmental-friendly materials and offer non-toxic and safe insulation solutions to industries.The company provides an extensive range of ceramic fiber boards with different densities, sizes, and thicknesses to suit various industries' needs. They specialize in customizing the ceramic fiber boards according to customers' specifications, including design, size, and shape.Their high-quality ceramic fiber boards are found in applications in industries such as power, metallurgy, chemical, and construction. The company has a proven track record of delivering cost-effective and innovative solutions to meet customers' demands. Their products are manufactured using trained personnel and the latest technology to ensure high-quality standards are met. The company's resources allow for a vast production capability, making them the ideal supplier for any industrial entity.In addition to the standard ceramic fiber boards, the company also offers ancillary products to enhance the boards' insulation efficiency. These include ceramic fiber insulation blankets, ceramic fiber papers, insulation textiles, ceramic fiber ropes, and ceramic fiber modules.The company's ceramic fiber boards are known for their superior quality, excellent insulation, and long life. Their boards have been tested and approved to be many times more durable than alternative insulation choices. This is a result of state-of-the-art manufacturing processes and materials.Moreover, the experienced team at the company ensures the products are delivered timely, and the customers' needs are met. The team is committed to providing fast and secure delivery services to ensure the customers' projects proceed smoothly.In conclusion, purchasing a ceramic fiber board from the company guarantees high-quality insulation solutions ideal for various industrial applications. The company's commitment to quality, innovation, and customer satisfaction is evident in the production and delivery of the ceramic fiber boards with excellent insulation properties. The company is driven by the goal of providing the best ceramic fiber boards to industries to enhance their efficiency and productivity, making them a reliable and reputable ceramic fiber board supplier. Therefore, if you need ceramic fiber boards, trust the leading industry veteran and take advantage of their expertise and specialized services. Contact the company today to ensure they meet all your insulation needs.
Get Top-Quality High Temperature Castable Refractory
Buy High Temperature Castable Refractory Boosts Industrial ProcessesCastable refractories have become a popular choice for industrial processes due to their excellent thermal properties. These materials are designed to withstand high temperatures and harsh conditions, making them ideal for use in furnaces, kilns, and other applications that involve extreme heat. Many industries rely on high temperature castables to optimize their manufacturing processes and extend the lifespan of their equipment. Therefore, leading manufacturers such as {remove brand name} offer a range of castable refractories to meet the diverse needs of their customers.One such product is high temperature castable refractory. This type of refractory is specially formulated to withstand temperatures above 3000°F. It is composed of a variety of raw materials, including high purity alumina, silicon carbide, and various binders. The combination of these components creates a refractory that is highly resistant to thermal shock, abrasion, and chemical attack. High temperature castables are commonly used in the steel, cement, glass, and petrochemical industries.In addition to its exceptional thermal properties, high temperature castable refractory has several advantages over traditional refractory materials. One such advantage is its ability to be cast into complex shapes. This allows manufacturers to create custom refractory linings that fit the exact specifications of their equipment. The castable nature of this refractory also makes it easy to install, reducing downtime and improving the efficiency of industrial processes.Another advantage of high temperature castables is their versatility. They can be used for a variety of applications, including furnace linings, burner blocks, and ladle linings. They are also suitable for use in a range of heating equipment, including kettles, crucibles, and incinerators. This makes them an ideal choice for industries that require high temperatures and need materials that can withstand harsh environments.{Remove brand name} is a leading manufacturer of high temperature castable refractory, offering a range of products that meet the diverse needs of their customers. Their castables are designed to provide exceptional performance in a range of applications, from steel and glassmaking to power generation and incineration. The company's castables are formulated with high purity raw materials and advanced binders, providing the optimal balance of strength and density.In addition to its high temperature castables, {remove brand name} offers a range of other refractory materials, including precast shapes, ceramic fiber products, and insulating materials. Their comprehensive product line makes them a one-stop-shop for industrial refractory needs, providing customers with the convenience of working with a single supplier.The company's dedication to quality is reflected in their ISO 9001 certification, which ensures that their castables and other refractory products meet the highest standards of quality. They also offer technical support and consultation services to help their customers identify the right refractory materials for their specific applications.In conclusion, high temperature castable refractory is an essential material for industries that require high-temperature resistance and durability in their industrial processes. {Remove brand name} is a leading provider of high-quality castable refractories, offering a comprehensive product line that meets the diverse needs of their customers. Their commitment to quality and customer service makes them a reliable partner for industries that rely on refractory materials to optimize their manufacturing processes.
High-Quality Fire Bricks for Industrial Applications
Silica Fire Brick Strengthens the Foundations of Industrial ApplicationsSilica fire bricks are quickly gaining popularity in the industrial sector due to their durability, strength, and resistance to high temperatures. These bricks are designed to withstand extreme temperature fluctuations and chemical corrosions, making them an ideal choice for industrial purposes.One of the leading producers of silica fire bricks is {company name}. The company has been in the industry for years, manufacturing premium quality fire bricks for use in various applications, including glassworks, non-ferrous metal melting, and steel plants, among others.Silica fire bricks are made from a mixture of high-purity silica, alumina, and other minerals that are carefully selected to ensure optimal performance. Once the raw materials are combined, they undergo a rigorous manufacturing process, including mixing, molding, and firing, to create a final product that is both strong and durable.{Company name} uses advanced technology and high-quality raw materials to manufacture silica fire bricks that meet and exceed industry standards. The company's fire bricks are designed to operate efficiently and last longer than traditional bricks, which can save industrial plant owners a substantial amount of money in the long run.The benefits of silica fire bricks are many. For one, they are known for their high thermal shock resistance and can withstand rapid temperature changes without cracking or breaking. This makes them an ideal choice for furnaces and kilns that are used to heat up materials to high temperatures.Silica fire bricks are also chemically inert, meaning they do not react with most substances. This makes them an excellent choice for lining chemical processing plants and other facilities where chemical reactions take place.Another advantage of using silica fire bricks is that they are highly durable. They can withstand wear and tear caused by temperature fluctuations, corrosive materials, and mechanical stress for extended periods. This makes them a cost-effective option for industrial plant owners who want to avoid frequent repairs and replacements.{Company name} is committed to producing high-quality silica fire bricks that are tailored to meet the specific needs of its clients. The company offers a range of product variations that are designed to work in different environments and under varying conditions. This ensures that clients get the best products for their industrial operations.{Company name} silica fire bricks are also eco-friendly. The company uses eco-friendly materials in the production process to minimize environmental damage. The manufacturing process is designed to ensure that waste is minimized, and the final products meet the industry's safety standards.In conclusion, silica fire bricks are a game-changer in the industrial sector. Their durability, strength, thermal shock resistance, and chemical inertness make them the perfect choice for a wide range of industrial applications. {Company name} is a leading producer of silica fire bricks that meet and exceed industry standards, offering clients customized solutions to meet their unique needs. With a commitment to quality, innovation, and eco-friendliness, {company name} is set to continue leading the way in the production of high-quality silica fire bricks.
Understanding the Importance of Arc Furnace Electrodes: A Comprehensive Guide
Title: Advancements in Arc Furnace Electrodes Facilitate Efficient Steel ProductionIntroduction:In the constantly evolving steel industry where efficiency and sustainability are key, companies are continuously seeking innovative solutions to optimize their production processes. One such groundbreaking advancement lies in the development of state-of-the-art arc furnace electrodes. These cutting-edge electrodes, produced by a renowned industry leader {}, are revolutionizing steelmaking and paving the way towards more efficient and eco-friendly practices.[Company Introduction - Approx. 200 words]Starting its journey in the early 1980s, {} has emerged as a global frontrunner in manufacturing arc furnace electrodes. Their unwavering commitment to excellence, extensive research and development, and supplier collaborations have propelled them to the forefront of the industry. With a reputation for consistently delivering quality products, they have earned the trust and loyalty of their customers worldwide.The company's modern facility, equipped with the latest manufacturing technologies and operated by highly skilled professionals, enables {} to produce high-performance arc furnace electrodes. These electrodes are essential components in the electric arc furnace (EAF) process, a widely adopted method for steel production due to its flexibility and cost-effectiveness.[Advancement 1 - Approx. 200 words]In a significant breakthrough, {} has successfully developed a next-generation arc furnace electrode that offers exceptional performance and durability. Through innovative design modifications and advancements in raw materials, these electrodes demonstrate improved electrical conductivity, thermal resistance, and resistance to oxidation. As a result, steelmakers can benefit from increased productivity, reduced energy consumption, and minimized downtime during the steelmaking process.The enhanced electrical conductivity of {}'s arc furnace electrodes allows for efficient transfer of electricity from the power source to the furnace, enabling faster melting rates and shorter cycle times. Consequently, steel manufacturers observe enhanced productivity and optimization of their manufacturing operations, leading to significant cost savings and increased profits.Additionally, the improved thermal resistance characteristic of these electrodes ensures stable and consistent heat transfer within the electric arc furnace, resulting in reduced melting time and increased overall energy efficiency. The reduction in energy consumption not only minimizes production costs but also aligns with the industry's focus on sustainability and environmental consciousness.[Advancement 2 - Approx. 200 words]Another breakthrough achieved by {} is the development of arc furnace electrodes with enhanced resistance to oxidation, thereby prolonging their lifespan. Through meticulous testing and optimization, the company has successfully formulated electrode compositions that exhibit superior resistance to oxidation even under extreme operating conditions. This advancement allows for longer electrode life, minimizing costly downtime associated with regular electrode replacements.The extended lifespan of {}'s arc furnace electrodes is particularly advantageous for steel manufacturers, as frequent electrode changes disrupt production flow and result in substantial economic losses. By offering electrodes with exceptional resistance to oxidation, the company enables seamless operations, providing steel producers with a competitive edge.Conclusion:With steel manufacturing being a vital industry worldwide, advancements in arc furnace electrodes play a pivotal role in optimizing steel production processes. Through their dedication to innovation and excellence, {} has emerged as a frontrunner in electrode manufacturing, introducing state-of-the-art products that enhance productivity, energy efficiency, and sustainability.The continuous evolution of arc furnace electrodes demonstrates the industry's commitment to pushing technological boundaries and meeting the ever-growing global demand for steel. As companies like {} continue to invest in research and development, the steel industry can look forward to more efficient, cost-effective, and eco-friendly steelmaking processes in the future.