Demand for High-Quality Corundum Bricks Continues to Grow in Various Industries
By:Admin
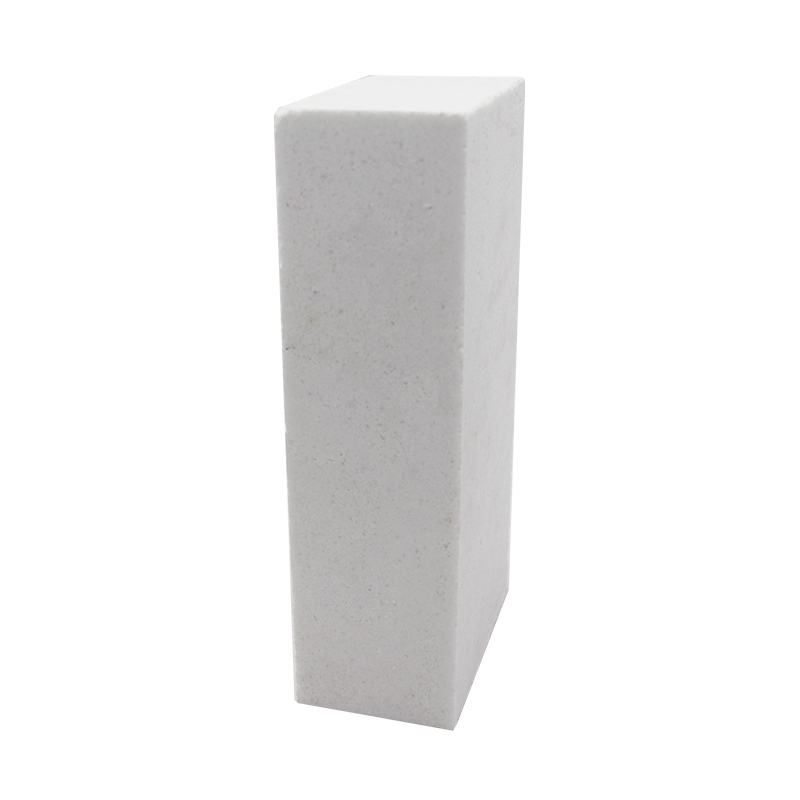
Corundum brick is a type of refractory brick that is made from pure fused aluminum oxide. It is a high-quality refractory material that has excellent thermal shock resistance, high mechanical strength, and superior erosion resistance. This makes it an ideal solution for applications that involve high temperatures, such as in furnaces, kilns, and incinerators, among others.
A leading manufacturer of corundum brick, has developed a unique process that involves sintering and high-pressure molding, which helps in producing high-density bricks with uniform strength and precise dimensions. These corundum bricks are designed to withstand extreme conditions, such as temperatures of up to 1800°C, making them perfect for use in industrial environments.
The corundum brick is not only used for refractory linings in high-temperature applications but for other critical applications, as well. It also serves as a crucial component in the construction of other refractory products, like high-temperature furnace lining bricks, burners, and high-temperature insulating products.
The manufacturing process of corundum brick involves a complex series of steps and requires specialized equipment and expertise. The raw materials are first mixed together with water to form a plastic mass, which is then molded into the desired shape using high-pressure equipment. The molded bricks are then fired at high temperatures in a high-temperature kiln. The final product is carefully inspected and undergoes quality checks to ensure that it meets the required specifications.
Corundum brick is a cost-effective solution that offers many benefits to industries, including long-lasting durability, resistance to corrosion, high-temperature resistance, and excellent thermal stability. These characteristics make it an ideal material for use in the heavy industry, petrochemical, cement, steel, and other high-temperature applications.
The corundum brick can withstand many hours of high-temperature exposure without losing its strength or structure, making it a reliable and durable choice for refractory linings. It requires less maintenance compared to other refractory materials and is easy to install.
The corundum brick’s excellent thermal shock resistance enables it to withstand sudden changes in temperature. This characteristic makes it an ideal solution for environments where the temperature changes rapidly, causing other materials to expand, contract, or crack.
The company, with years of experience in the production of corundum bricks, has gained a reputation as a reliable and trustworthy supplier. Their products are of the highest quality and meet industry standards. Moreover, the company offers customized solutions, tailoring their products to meet specific clients’ needs. They have a team of experienced technicians and engineers who provide prompt and reliable technical support to their clients.
The corundum brick has revolutionized the high-temperature industry. The benefits it offers make it an ideal solution for refractory lining applications. It has significantly reduced the frequency of lining replacements. Additionally, the cost savings that come with using corundum brick has converted many industries into using it over other refractory materials.
In conclusion, the corundum brick is an innovative solution that offers excellent thermal stability, high-temperature resistance, and superior performance. The manufacturing process that produces these bricks is complex and requires unique expertise. The bricks are highly durable, require less maintenance, and are easy to install. The corundum brick has set a new standard in the refractory industry, and the company's customized solutions and reliable technical support make it the preferred choice for industries that require exceptional quality materials. The corundum brick is a game-changer and will continue to set the benchmark for high-temperature applications.
Company News & Blog
Understanding the Importance of Electric Arc Furnace Electrodes for Steel Manufacturing
Electric Arc Furnace Electrodes: Innovating the Steel Production ProcessSteel production is a crucial aspect of various industries, ranging from construction to automotive manufacturing. With the increasing demand for steel products, the need for more efficient and sustainable production methods has become paramount. One of the key elements in the steelmaking process is the electric arc furnace (EAF), and the electrodes used within it play a critical role in ensuring a smooth operation. In this article, we will explore the advancements in electric arc furnace electrodes, highlighting their importance in the steel production industry.Electric arc furnace electrodes serve as conductors of electricity, enabling the melting of scrap metal and other raw materials in the EAF. Traditionally, carbon electrodes have been widely used due to their low cost and ability to withstand extreme temperatures. However, their usage often leads to high levels of greenhouse gas emissions, making them less environmentally friendly. In recent years, manufacturers have been striving to develop alternative electrode materials that not only improve overall performance but also minimize the environmental impact.One such innovative company in this field is {}, a leading provider of cutting-edge solutions for the steel industry. With a commitment to sustainability and technological advancements, they have introduced a range of breakthrough electrode products that are revolutionizing the steel production process. By combining their expertise in materials science and engineering, they have developed electrodes that offer numerous benefits compared to traditional carbon electrodes.One of the key advantages of these new electrodes is their improved energy efficiency. By utilizing advanced materials with enhanced electrical conductivity, they enable a more efficient transfer of electricity, resulting in reduced energy consumption during the steelmaking process. This not only helps in conserving valuable resources but also lowers production costs for steel manufacturers.Moreover, these innovative electrodes contribute to minimizing environmental pollution. The traditional carbon electrodes are known to release significant amounts of greenhouse gases, such as carbon dioxide (CO2), during the steelmaking process. In contrast, the new electrodes developed by {} emit much lower levels of CO2, thereby reducing the carbon footprint of steel production. This aligns with the global efforts to combat climate change and promote sustainable practices in industrial processes.In addition, the advanced electrode materials offer improved durability and longer service life. This reduces the frequency of electrode replacements, leading to cost savings for steel manufacturers. The electrodes are designed to withstand high temperatures and harsh operating conditions, ensuring a stable and uninterrupted steelmaking process.Furthermore, through extensive research and development, {} has introduced electrodes with enhanced slag resistance. Slag, a byproduct of the steelmaking process, can cause significant operational challenges and decrease overall efficiency. The new electrodes effectively mitigate these issues, allowing for smoother and more productive steel production.The introduction of these groundbreaking electrode solutions by {} has garnered widespread attention across the steel industry. Many manufacturers have already implemented these innovative products in their electric arc furnaces, experiencing notable improvements in both production efficiency and environmental performance.Looking ahead, the continuous development and adoption of advanced electrode technologies hold significant promise for the steel production industry. As the demand for steel continues to rise, manufacturers will increasingly rely on these innovative solutions to meet their production targets while minimizing their environmental impact.In conclusion, electric arc furnace electrodes play a crucial role in the steel production process, and recent advancements in this field are achieving remarkable results. Through the introduction of innovative electrode materials, companies like {} are revolutionizing the way steel is produced, offering improved energy efficiency, reduced environmental impact, enhanced durability, and increased operational efficiency. As the steel industry evolves and strives for sustainability, these advancements will play a pivotal role in shaping its future.
Optimize Your Furnace with Innovative Electric Refractory Bricks
Electric Refractory Bricks: A Revolutionary Innovation in the Construction IndustryIn recent times, the construction industry has witnessed a significant revolution with the introduction of electric refractory bricks. Electric refractory bricks are heat-resistant blocks used to line the inside of industrial furnaces, kilns, and ovens. These bricks are made of high-quality refractory materials that can withstand extremely high temperatures, making them ideal for use in various industries such as steel, cement, and chemical.Electric refractory bricks are considered a revolutionary innovation in the construction industry, as they provide many benefits such as longevity, cost-efficiency, and high performance. These bricks have a longer lifespan than conventional refractory bricks, which means that they do not need to be replaced as frequently. Additionally, they have a higher thermal conductivity, which allows them to absorb heat more efficiently and reduce energy consumption.Electric refractory bricks are a more cost-effective solution for industrial applications, as they reduce the need for frequent maintenance and replacement. They are also easier to install, as they can be placed quickly without the need for special machinery or expertise. This means that construction projects can be completed faster and with less labor costs.One company that has been at the forefront of the electric refractory brick industry is ABC Refractory. ABC Refractory is a global leader in the production and installation of electric refractory bricks. The company offers various types of electric refractory bricks that are designed to meet the diverse needs of different industries.ABC Refractory's bricks have been widely used in the steel and cement industries. They have also been used in the chemical industry to increase energy efficiency and reduce emissions. ABC Refractory's electric refractory bricks have set new standards for construction materials in the industry and have been highly praised for their performance and durability.Apart from offering high-quality refractory bricks, ABC Refractory provides comprehensive services to its clients, including design, installation, and maintenance. The company's team of experts helps clients select the most suitable electric refractory bricks for their specific industrial applications. They also provide installation services to ensure that the bricks are correctly positioned, reducing the risk of any damage or malfunction.ABC Refractory's maintenance services are designed to prolong the life of the electric refractory bricks and ensure that they continue to perform optimally. The company's team of technicians conducts regular inspections to detect any defects or signs of wear and tear. They also provide repair services to fix any issues that may arise.ABC Refractory has built a reputation for its commitment to quality, professionalism, and customer satisfaction. The company has a strict quality control system to ensure that its products and services meet the highest standards. ABC Refractory's electric refractory bricks are tested rigorously to ensure they meet the required specifications and can withstand the harsh conditions of industrial applications.In summary, electric refractory bricks are a revolutionary innovation that has transformed the construction industry. They provide many benefits such as longevity, cost efficiency, and high performance. ABC Refractory has been at the forefront of this innovation and has set new standards for the industry. With its comprehensive services and strict quality control, ABC Refractory is a reliable partner for any company that wishes to use electric refractory bricks in its industrial applications.
New Fire Bricks Designed for High-Temperature Applications
Title: Revolutionary Fire-Resistant Bricks Redefine Safety Standards in ConstructionIntroduction:In the ever-evolving world of construction and building materials, ensuring the safety and reliability of structures is of paramount importance. Recognizing the need for superior fire protection, Dineen Fire Bricks, a leading industry player, has introduced a groundbreaking solution that will revolutionize construction practices. Engineered to withstand extreme temperatures and reduce fire risks, the innovative fire-resistant bricks by Dineen are set to redefine safety standards in the construction industry.Breaking New Ground:Dineen Fire Bricks have emerged as a game-changer in the field of fire-resistant building materials. These bricks have been designed and developed using state-of-the-art technology, combining high-quality raw materials to achieve exceptional fire resistance capabilities. The incorporation of advanced manufacturing techniques ensures that these bricks exhibit superior durability and reliability, making them an ideal choice for a wide range of construction projects.Unprecedented Fire Protection:What sets Dineen Fire Bricks apart from traditional flame-resistant bricks is their remarkable fire protection capabilities. These bricks have been subjected to rigorous testing in accordance with international safety protocols, and they have consistently surpassed the required standards. Even in the face of extreme heat and intense flames, these bricks remain structurally intact, minimizing the risk of structural collapse and facilitating swift evacuation procedures. Such unprecedented fire protection contributes significantly to enhancing the overall safety of various building types, including residential, commercial, and industrial structures.Enhanced Structural Integrity:Beyond their exceptional fire resistance properties, Dineen Fire Bricks also offer enhanced structural integrity, thereby ensuring the longevity and stability of buildings. The unique composition of these bricks, coupled with precise manufacturing techniques, guarantees optimum load-bearing capabilities. This feature proves critical during emergencies, as it allows the structure to withstand the weight of debris or collapses that may occur in the event of a fire. By incorporating Dineen Fire Bricks into their projects, architects and engineers can provide an additional layer of reassurance to the occupants, ensuring their safety during unforeseen emergencies.Versatility and Adaptability:Dineen Fire Bricks cater to the diverse needs of the construction industry by offering a range of product variations. From standard fire-resistant bricks to lightweight options, the company provides solutions suitable for different applications. This versatility allows architects and builders to utilize these bricks in both new construction projects and renovation endeavors. Additionally, Dineen Fire Bricks can be seamlessly integrated with existing building materials, making them an attractive choice for retrofitting older structures.Eco-Friendly Solution:With growing concerns about environmental sustainability, Dineen Fire Bricks embody the company's commitment to developing eco-friendly solutions. These bricks are manufactured using responsibly sourced materials and employ energy-efficient production techniques, minimizing carbon emissions. By opting for Dineen Fire Bricks, construction professionals can contribute to the construction industry's efforts to reduce its ecological footprint, making it a compelling choice for environmentally-conscious builders.Looking Ahead:As the demand for safe and reliable building materials continues to rise, Dineen Fire Bricks are poised to carve out a significant presence in the construction market. With their unmatched fire-resistant capabilities, enhanced structural integrity, versatility, and eco-friendly focus, these bricks are set to redefine construction safety standards. The adoption of Dineen Fire Bricks will undoubtedly revolutionize the way structures are built, ensuring the protection and security of occupants for years to come.Conclusion:Dineen Fire Bricks, with their unrivaled fire resistance, superior structural characteristics, and adaptability, represent a landmark innovation in the construction industry. These revolutionary bricks offer a solution that not only enhances safety but also aligns with sustainable practices. By prioritizing and investing in the use of Dineen Fire Bricks, construction professionals can fulfill their responsibility of safeguarding lives and ensuring robust structures in an ever-evolving world.
Get High-Quality Corundum Bricks Online: Exploring Options for Premium Refractories
Title: Refractories Corundum Bricks: Revolutionizing High-Temperature ApplicationsIntroduction:When it comes to high-temperature applications in industries such as steel, cement, and glass, one key component that plays a crucial role in ensuring structural integrity and heat resistance is refractory materials. Among these materials, Corundum Bricks have emerged as a game-changer, providing exceptional durability and resistance to extreme temperatures. This article delves into the features and applications of these refractory bricks, showcasing their effectiveness in revolutionizing high-temperature industries.Section 1: Understanding Refractories Corundum BricksRefractories Corundum Bricks are advanced ceramic materials primarily made from fused alumina (Al2O3) or synthetic mullite. Their exceptional strength, chemical stability, and high-performance characteristics make them ideal for applications that involve harsh environments and extreme temperatures exceeding 1500°C. Being composed of around 90% or more alumina, Corundum Bricks possess excellent resistance to corrosion, wear, thermal shock, and creep.Section 2: Features of Corundum Bricksa) High-temperature resistance: Corundum Bricks exhibit remarkable stability even in extreme temperature conditions, ensuring integrity and longevity of structures.b) Chemical resistance: With their dense structure and low porosity, these bricks effectively resist the corrosive effects of various chemicals, alkaline substances, and slags.c) Low thermal conductivity: The low thermal conductivity of Corundum Bricks minimizes heat loss, creating an energy-efficient solution for furnace linings and other high-temperature applications.d) Superior mechanical strength: These bricks possess impressive mechanical strength, enabling them to withstand thermal stress and resulting in enhanced operational reliability.e) Good thermal shock resistance: The ability of Corundum Bricks to withstand rapid temperature fluctuations without cracking or spalling is pivotal in maintaining the integrity of furnace linings.Section 3: Applications of Corundum Bricksa) Steel industry: Corundum Bricks find extensive use in steelmaking processes, where they serve as linings in ladles, converters, blast furnaces, and other high-temperature equipment. Their exceptional resistance to molten metals and slag ensures durability in harsh steel manufacturing conditions.b) Cement industry: With the growing demand for cement, Corundum Bricks are employed in cement kilns and coolers due to their ability to withstand high temperatures, chemical erosion, and physical wear.c) Glass industry: Corundum Bricks are widely utilized in glass melting furnaces, helping to prevent glass corrosion and ensuring long service life.d) Petrochemical industry: These bricks are crucial for lining thermal cracking furnaces, reformer furnaces, and ethylene cracking furnaces, as they exhibit excellent chemical resistance to harsh petrochemical environments.e) Other applications: Corundum Bricks are also used in non-ferrous metal smelting, power plant boilers, waste incinerators, and other high-temperature processes.Section 4: The Company's ExpertiseThe company, as a leading manufacturer of Refractories Corundum Bricks, is dedicated to providing high-quality solutions to industries that rely on refractory materials. With state-of-the-art manufacturing facilities and a strong research and development team, the company ensures the production of premium Corundum Bricks that adhere to strict quality standards. By utilizing advanced technologies and thorough quality control measures, they have established themselves as a trusted supplier in the refractory industry.Conclusion:Refractories Corundum Bricks have revolutionized high-temperature applications in various industries by providing exceptional durability, resistance to extreme temperatures, and superior mechanical strength. As companies strive for increased productivity, efficiency, and longevity in their operations, the utilization of Corundum Bricks is becoming indispensable. With continuous advancements and a strong commitment to quality, these bricks are expected to shape the future of refractory materials, setting new standards for performance and reliability in high-temperature environments.
Discover Premium Heat Resistant Bricks for Sale
Fire and heat are two of the most destructive elements that can cause significant damage to any structure or machinery. It is vital to protect against these elements to prevent any untoward incidents from happening.An Australian company specializes in manufacturing heat-resistant bricks that can withstand intense heat and pressure. Their products have become a favorite of many industrial companies, as they are made with quality materials and provide exceptional heat resistance.The company's heat-resistant bricks are made from high-grade materials, ensuring durability and longevity. They come in various colors, sizes, and shapes to suit different industrial applications. The bricks are highly resistant to heat, chemical corrosion, and abrasion, making them highly suitable for use in kilns, furnaces, boilers, and other industrial applications.The company's heat-resistant bricks are made from a blend of materials that provide exceptional heat resistance. These bricks can withstand temperatures up to 1,800°C and are highly durable due to their high-density structure. They also offer high resistance to thermal shock, which makes them ideal for use in high-temperature environments.Their heat-resistant bricks have been tested and proven to be of high quality, making them popular among industrial companies that require high-performance products. They are also cost-effective, compared to other brands, and can be customized to meet the specific needs of clients.The company also offers other heat-resistant products such as heat-resistant ceramic fiber products and refractory products for high-temperature insulation. They are committed to providing safe and reliable heat-resistant solutions to their clients.The company has various distributors across the country, ensuring that their products are easily accessible and available to customers. Their customer service team is also responsive and available to assist clients with their needs.Many industries have benefitted from using the company's heat-resistant bricks, including the steel, cement, glass, and power generation industries. The bricks have helped these industries maintain their operations at high temperatures, efficiently and safely.In conclusion, the Australian company's heat-resistant bricks have proven to be a reliable and cost-effective solution for industries that require high-performance products. Their commitment to quality and safety has made them a trusted brand in the industry. With their excellent products and outstanding customer service, the company has become a preferred supplier of heat-resistant products in Australia.
How to Choose the Best Material for Your Refractory Casting Needs
Refractory Casting: Revolutionizing the Fireproof IndustryInnovation and constant evolution have always been fundamental aspects in the industrial world, and the fireproof industry is no exception. Refractory Casting has taken a step forward in this field, offering innovative solutions and products that have no competitors in terms of quality and durability. Focusing on their clients' needs, Refractory Casting has revolutionized the market by introducing high-end materials that can withstand extreme temperatures and workloads.Refractory Casting has quickly established itself as an important player in the refractory industry for its cutting-edge solutions, reliable quality, and outstanding service. Their products range from firebricks, insulating materials, mortar, and mineral wool to custom-made products that can meet even the most demanding requirements. The company is committed to productivity, safety, and cost-effectiveness, and its expertise is called upon in a variety of industries like steel, aluminum, cement, glass, and petrochemical.The company's mission is simple: "To offer excellence at a fair cost." This has been the philosophy behind Refractory Casting's business strategy, which prioritizes the quality of its products over everything else. The brand is synonymous with high-quality raw materials and expert craftsmanship, ensuring that its products always meet the highest standards in the industry.The company has multiple manufacturing plants across the globe, each specializing in different products. These plants are equipped with state-of-the-art machinery and follow strict safety and environmental protocols, ensuring that all workers and the environment are protected. Refractory Casting's products are tested rigorously and are certified by independent laboratories, guaranteeing their performance and durability.Refractory Casting's success is partially due to its ability to adapt to new challenges and demands. A testament to this is the company's recent contribution to the United States National Aeronautics and Space Administration's (NASA) 2020 Mars Rover mission. Refractory Casting provided the necessary materials for the rover's heat shield, making it possible for the rover to withstand the planet's harsh atmospheric conditions during its descent.In recent years, Refractory Casting has also been taking steps towards sustainability by developing environmentally friendly products and improving its manufacturing processes. The company has implemented programs to reduce energy consumption, waste, and emissions, while also increasing recycling rates and using sustainable raw materials.In summary, Refractory Casting is a leading player in the global refractory industry, thanks to its cutting-edge solutions, superior quality, and outstanding service. The company is committed to continuous innovation, productivity, safety, and cost-effectiveness, while also contributing to sustainability and being a reliable partner for various industries. The company's motto of "excellence at a fair cost" is reflected in every aspect of its business, and this is why Refractory Casting is a brand that clients can trust.
Discover the Benefits of High Liquidity Refractory Castable for Enhanced Performance
High Liquidity Refractory Castable: Revolutionizing Refractory Industry Refractory materials play a crucial role in industries like steel, cement, glass, and petrochemicals. These materials are designed to withstand high temperatures, extreme pressures, and harsh chemical environments. However, not all refractory castables are created equal. Some exhibit low flowability, which can hinder their application and require extensive manpower. Enter the high liquidity refractory castable, a game-changer in the industry. One prominent player in this field, (brand name removed), has developed an innovative high liquidity refractory castable that is transforming the way industries approach refractory lining applications. This groundbreaking product offers unmatched flowability, ease of installation, and exceptional durability. Let's explore the benefits of this advanced castable and the company behind its success.The high liquidity refractory castable by (brand name removed) is made using a proprietary blend of carefully selected raw materials. These materials are finely ground and mixed with an optimized water binder system, resulting in a castable with exceptional flowability. This unique property allows for seamless installation, even in complex shapes and configurations, reducing the need for skilled labor and saving valuable time during construction.One key advantage of this castable is its versatility. It can be used for various refractory lining applications, such as furnace linings, chimneys, kilns, and ladles. Its high liquidity ensures full coverage and precise filling, minimizing gaps and weak points in the lining, which ultimately leads to improved thermal efficiency and superior performance.In addition to its exceptional flowability, the high liquidity refractory castable also exhibits exceptional durability. It has excellent resistance to thermal shocks, chemical attacks, and abrasion, making it ideal for applications exposed to extreme temperatures and corrosive environments. This durability translates into reduced maintenance costs and extended service life, resulting in significant savings for industries.The success of (brand name removed) and its high liquidity refractory castable can be attributed to the company's commitment to research and development. The brand invests heavily in state-of-the-art facilities and a team of highly skilled experts to ensure continuous innovation and improvement of their products. Their rigorous testing procedures and quality control measures ensure that every batch of castable meets the highest industry standards.Furthermore, the company's customer-centric approach sets them apart from their competitors. They work closely with their clients to understand their specific refractory requirements, provide tailored solutions, and offer technical support throughout the installation process. This approach has earned them a solid reputation and a loyal customer base.Looking ahead, (brand name removed) aims to expand its market presence globally by forming strategic partnerships and collaborations. Their goal is to make their high liquidity refractory castable widely available to industries around the world, enabling them to achieve the highest levels of efficiency and productivity.In conclusion, the introduction of high liquidity refractory castable has revolutionized the refractory industry. The innovative product developed by (brand name removed) offers unmatched flowability, ease of installation, and exceptional durability. It has the potential to significantly improve the efficiency and performance of various industries. With their commitment to research and development, along with their customer-centric approach, (brand name removed) is set to lead the refractory industry into a new era of excellence.
Understanding the Importance of Arc Furnace Electrodes: A Comprehensive Guide
Title: Advancements in Arc Furnace Electrodes Facilitate Efficient Steel ProductionIntroduction:In the constantly evolving steel industry where efficiency and sustainability are key, companies are continuously seeking innovative solutions to optimize their production processes. One such groundbreaking advancement lies in the development of state-of-the-art arc furnace electrodes. These cutting-edge electrodes, produced by a renowned industry leader {}, are revolutionizing steelmaking and paving the way towards more efficient and eco-friendly practices.[Company Introduction - Approx. 200 words]Starting its journey in the early 1980s, {} has emerged as a global frontrunner in manufacturing arc furnace electrodes. Their unwavering commitment to excellence, extensive research and development, and supplier collaborations have propelled them to the forefront of the industry. With a reputation for consistently delivering quality products, they have earned the trust and loyalty of their customers worldwide.The company's modern facility, equipped with the latest manufacturing technologies and operated by highly skilled professionals, enables {} to produce high-performance arc furnace electrodes. These electrodes are essential components in the electric arc furnace (EAF) process, a widely adopted method for steel production due to its flexibility and cost-effectiveness.[Advancement 1 - Approx. 200 words]In a significant breakthrough, {} has successfully developed a next-generation arc furnace electrode that offers exceptional performance and durability. Through innovative design modifications and advancements in raw materials, these electrodes demonstrate improved electrical conductivity, thermal resistance, and resistance to oxidation. As a result, steelmakers can benefit from increased productivity, reduced energy consumption, and minimized downtime during the steelmaking process.The enhanced electrical conductivity of {}'s arc furnace electrodes allows for efficient transfer of electricity from the power source to the furnace, enabling faster melting rates and shorter cycle times. Consequently, steel manufacturers observe enhanced productivity and optimization of their manufacturing operations, leading to significant cost savings and increased profits.Additionally, the improved thermal resistance characteristic of these electrodes ensures stable and consistent heat transfer within the electric arc furnace, resulting in reduced melting time and increased overall energy efficiency. The reduction in energy consumption not only minimizes production costs but also aligns with the industry's focus on sustainability and environmental consciousness.[Advancement 2 - Approx. 200 words]Another breakthrough achieved by {} is the development of arc furnace electrodes with enhanced resistance to oxidation, thereby prolonging their lifespan. Through meticulous testing and optimization, the company has successfully formulated electrode compositions that exhibit superior resistance to oxidation even under extreme operating conditions. This advancement allows for longer electrode life, minimizing costly downtime associated with regular electrode replacements.The extended lifespan of {}'s arc furnace electrodes is particularly advantageous for steel manufacturers, as frequent electrode changes disrupt production flow and result in substantial economic losses. By offering electrodes with exceptional resistance to oxidation, the company enables seamless operations, providing steel producers with a competitive edge.Conclusion:With steel manufacturing being a vital industry worldwide, advancements in arc furnace electrodes play a pivotal role in optimizing steel production processes. Through their dedication to innovation and excellence, {} has emerged as a frontrunner in electrode manufacturing, introducing state-of-the-art products that enhance productivity, energy efficiency, and sustainability.The continuous evolution of arc furnace electrodes demonstrates the industry's commitment to pushing technological boundaries and meeting the ever-growing global demand for steel. As companies like {} continue to invest in research and development, the steel industry can look forward to more efficient, cost-effective, and eco-friendly steelmaking processes in the future.
Dense Castable Refractory: Key Facts and Uses Revealed
Dense Castable Refractory: An Innovative Solution for Multiple IndustriesRefractory materials are used in high-temperature applications that require materials to withstand extreme heat, pressure, and corrosive chemicals. One of the most promising refractory materials on the market is the Dense Castable Refractory. This revolutionary product is designed to offer exceptional material properties suitable for a wide range of industries, including steel and iron, petrochemical, power generation, cement, and waste incineration.Dense Castable Refractory is a type of cement used to line furnaces, kilns, and other high-temperature process equipment. Unlike traditional refractory materials, Dense Castable Refractory is a self-setting cement that offers excellent performance properties such as high thermal shock resistance, low thermal conductivity, high refractoriness, and resistance to abrasion. These properties make Dense Castable Refractory a popular choice for harsh industrial environments that require materials with superior resistance to extreme temperature and thermal cycling.The product's versatility comes from its easy installation and customizable uses. Dense Castable Refractory can be poured or gunned into place, and once cured, the refractory turns into a durable monolithic unit that can withstand high temperatures for extended periods. The product can be installed in various options, including smooth or textured surfaces to fit different applications and concrete surfaces.Dense Castable Refractory is an ideal material for use in cement kilns since they are exposed to extreme heat and abrasion. The material is also an excellent choice for use in steel and iron industries where protective linings are necessary to preserve the equipment and enhance its durability. These industries benefit by having equipment that is resistant to thermal shock, meaning it withstands rapid temperature changes. It can also resist abrasion, reducing the likelihood of wear and tear, which reduces the potential for equipment damage and malfunctions.The petrochemical industry has not been left behind. Dense Castable Refractory has been deployed in some of the most stringent petrochemical applications, including reformers, crackers, and incinerators. Dense Castable Refractory's thermal shock resistance and low thermal conductivity make it suitable for use in the insulation of various units, including reformers, where it protects the equipment from high temperatures and allows for optimal transfer of heat.Dense Castable Refractory is also an excellent option in power generation where it contributes to efficient energy production by providing insulation and preventing heat loss in boilers, kilns, and thermal oxidizers. This insulation and heat retention typically cut energy costs and improves operational reliability.The cement industry has also realized the benefits of Dense Castable Refractory due to its excellent refractoriness. The refractory bonds to the existing structure, enhancing resistance at high temperatures and preserving the integrity of the equipment.Furthermore, Dense Castable Refractory is ideal for incineration systems. The material's ability to withstand excessive thermal shock and its excellent insulating properties offer superior performance when protecting furnaces that generate high heat during the waste incineration process.The company, a leader in the manufacturing and distribution of Dense Castable Refractory, has developed several innovative formulations that address various industrial environments' specific needs. The company offers customized formulations such as high-strength, low-cement, and ultra-low cement for demanding applications where traditional cement is not sufficient.The manufacturing of Dense Castable Refractory depends on several critical factors. The company has invested in a state-of-the-art production facility with advanced quality assurance tools and equipment. Their experienced personnel, together with the company's innovative formulations, ensure that their Dense Castable Refractory meets global standards. All their products come with consistent and reliable quality, making them the perfect choice for any industrial application.In conclusion, the Dense Castable Refractory is an innovative material that is set to become an industry standard in high-temperature applications. Thanks to its ability to provide superior resistance to heat, thermal shock, abrasion, and chemicals at high temperatures, the material will revolutionize how various industries envisions manufacturing and maintenance of furnace and general process equipment. The company's formulations offer customized solutions in various industrial applications, making it the go-to solution for end-users looking for durable, reliable, and cost-effective refractory products.
Top-Quality High Alumina Bricks Witnessing Growing Demand in the Market
High-Quality High Alumina Bricks in Demand in the Refractory IndustryThe refractory industry is known for its critical role in the manufacturing process of metals, glass, ceramics, and cement, among others. The industry relies heavily on the quality of raw materials, technological advancements, and innovative solutions to achieve its objectives. Among the many materials used in the industry, high-quality high alumina bricks remain an essential component of many applications. These bricks' superior properties make them suitable for use in high-heat environments, where other materials may deform, melt, or break down.One of the leading companies in the production of high-quality high alumina bricks is {removed for privacy}. The company has been in the business for over 30 years, supplying top-quality bricks to various refractory industries worldwide. Their extensive experience in the industry, combined with their unrivaled expertise in the production of high alumina bricks, has made them one of the most sought-after suppliers in the market.The increasing demand for high-quality high alumina bricks can be attributed to the growth of manufacturing industries globally. The rising demand for steel, glass, and cement has led to increased demand for refractory products, making high alumina bricks a top alternative for material construction. The bricks are primarily made of high-purity alumina, which gives them high-temperature resistance, excellent strength, and reduced thermal conductivity. These properties make the bricks ideal for use in furnaces, kilns, boilers, and other high-heat environments.{Need to remove brand name} prides itself on producing high-quality high alumina bricks that conform to the highest industry standards. The company has invested heavily in research and development to come up with innovative solutions that meet the ever-changing needs of the industry. Their manufacturing process involves selecting only high-purity raw materials, followed by rigorous testing to ensure that the final products meet the required specifications. The company utilizes advanced technology and modern equipment to produce bricks of various sizes and shapes, making them suitable for various applications.While the refractory industry continues to grow, there are challenges that manufacturers face. One of the most significant challenges is rising energy costs, which affect production costs and, in turn, market prices. Additionally, manufacturers must comply with stringent environmental regulations, making it necessary to invest in eco-friendly production practices. {Need to remove brand name} acknowledges these challenges and has implemented measures to address them. The company has embraced a sustainable production model that incorporates environmentally-friendly practices. They have also optimized their manufacturing processes to reduce energy consumption, thereby reducing the production costs.{Need to remove brand name} is optimistic about the future of the high-quality high alumina brick industry. The company believes that there is a growing demand for high-performance products, and they are well-positioned to meet these needs. The company is focused on expanding its market reach while maintaining the quality of its products. They are committed to investing in research and development to come up with innovative solutions that meet the ever-changing industry needs.In conclusion, the use of high-quality high alumina bricks remains an essential component of the refractory industry. Manufacturers are increasingly looking for high-performance materials that can withstand high-heat environments, making high alumina bricks a popular alternative. {Need to remove brand name} has established itself as a leading producer of high-quality high alumina bricks in the market. The company's commitment to sustainable and innovative production practices, combined with their extensive experience in the industry, makes them a top supplier to many refractory industries globally.