High Temperature Resistant Insulation Board for Industrial Applications
By:Admin
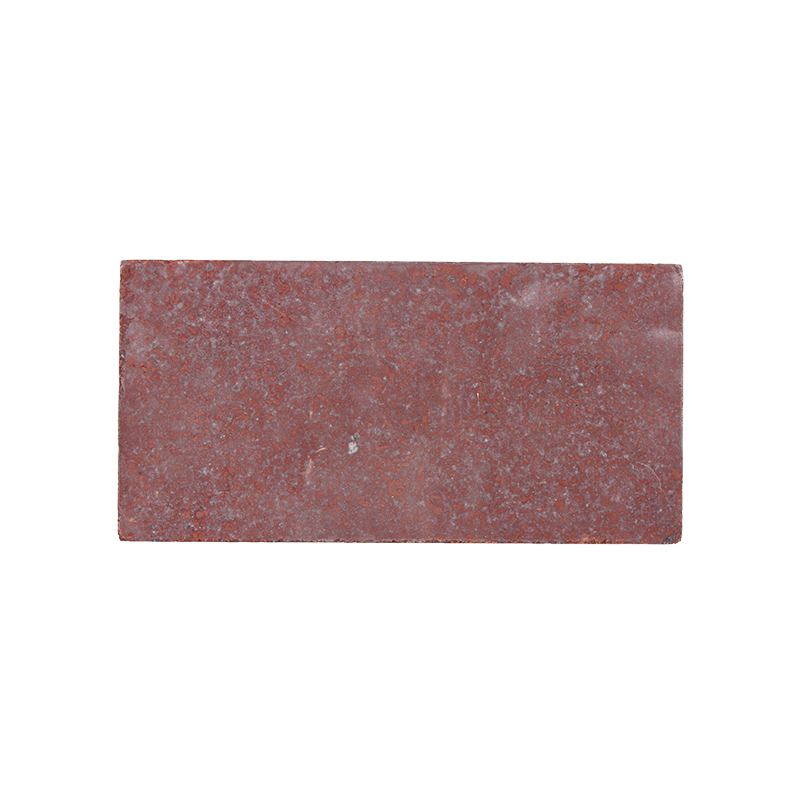
Introducing a revolutionary product in thermal insulation - Ceramic Fiber Insulation Board! Designed with cutting-edge technology, this new solution promises to set new standards in thermal protection. Developed by an industry-leading company known for its innovative products, this state-of-the-art board offers exceptional performance, efficiency, and durability.
With rapid advancements in technology, the need for effective thermal insulation has become paramount across various industries. From aerospace and automotive to manufacturing and construction, businesses are constantly searching for reliable ways to protect their premises and equipment from excessive heat and energy loss. Recognizing this need, the renowned company has developed the Ceramic Fiber Insulation Board, which boasts superior thermal insulation capabilities.
Made from high-quality ceramic fibers, this insulation board exhibits remarkable heat resistance and low thermal conductivity. Its unique composition enables it to withstand extreme temperatures, making it an ideal choice for applications where heat preservation and management are vital. By effectively trapping the heat within the designated area, this board can significantly reduce energy consumption and prevent heat loss, thereby saving costs and improving overall efficiency.
The Ceramic Fiber Insulation Board offers a plethora of advantages, making it an exceptional product in the market. Its lightweight and flexible nature allow for easy installation and handling, enabling businesses to expedite their project timelines. Furthermore, its versatility allows it to be used across various industries and applications. From lining industrial furnaces and kilns to insulating pipes, tanks, and chimneys, this board can deliver exceptional performance in almost any setting.
The use of Ceramic Fiber Insulation Board can also contribute to a safer working environment. With its excellent thermal stability and resistance to thermal shocks, this product minimizes the risk of accidents caused by sudden temperature changes and thermal stress. By creating a stable and secure environment, businesses can ensure the safety of their employees and protect their valuable assets.
In addition to its thermal insulation properties, the Ceramic Fiber Insulation Board is also known for its sound absorption capabilities. By reducing noise pollution and preventing sound amplification, this board can contribute to a more peaceful and productive working environment. This remarkable feature makes it particularly suitable for applications where noise control is crucial, such as power plants or manufacturing facilities.
Featuring a durable construction, the Ceramic Fiber Insulation Board offers long-lasting performance, even in harsh conditions. Its resistance to chemical corrosion and erosion ensures that it can withstand the test of time, providing businesses with reliable thermal insulation for years to come. This durability further enhances its cost-effectiveness, as frequent replacements and maintenance are minimized.
To ensure that the Ceramic Fiber Insulation Board meets the highest safety and quality standards, it has undergone rigorous testing procedures. Compliance with industry regulations and certifications highlights the commitment of the company towards manufacturing products that prioritize safety and reliability.
As businesses strive to improve energy efficiency and enhance productivity, the Ceramic Fiber Insulation Board emerges as an ideal solution. With its exceptional thermal insulation properties, durability, and versatility, this groundbreaking product is set to transform the way industries protect themselves against excessive heat and energy loss. Embrace the future of thermal insulation with Ceramic Fiber Insulation Board and unlock a world of possibilities for your business.
Company News & Blog
New Fire Bricks Designed for High-Temperature Applications
Title: Revolutionary Fire-Resistant Bricks Redefine Safety Standards in ConstructionIntroduction:In the ever-evolving world of construction and building materials, ensuring the safety and reliability of structures is of paramount importance. Recognizing the need for superior fire protection, Dineen Fire Bricks, a leading industry player, has introduced a groundbreaking solution that will revolutionize construction practices. Engineered to withstand extreme temperatures and reduce fire risks, the innovative fire-resistant bricks by Dineen are set to redefine safety standards in the construction industry.Breaking New Ground:Dineen Fire Bricks have emerged as a game-changer in the field of fire-resistant building materials. These bricks have been designed and developed using state-of-the-art technology, combining high-quality raw materials to achieve exceptional fire resistance capabilities. The incorporation of advanced manufacturing techniques ensures that these bricks exhibit superior durability and reliability, making them an ideal choice for a wide range of construction projects.Unprecedented Fire Protection:What sets Dineen Fire Bricks apart from traditional flame-resistant bricks is their remarkable fire protection capabilities. These bricks have been subjected to rigorous testing in accordance with international safety protocols, and they have consistently surpassed the required standards. Even in the face of extreme heat and intense flames, these bricks remain structurally intact, minimizing the risk of structural collapse and facilitating swift evacuation procedures. Such unprecedented fire protection contributes significantly to enhancing the overall safety of various building types, including residential, commercial, and industrial structures.Enhanced Structural Integrity:Beyond their exceptional fire resistance properties, Dineen Fire Bricks also offer enhanced structural integrity, thereby ensuring the longevity and stability of buildings. The unique composition of these bricks, coupled with precise manufacturing techniques, guarantees optimum load-bearing capabilities. This feature proves critical during emergencies, as it allows the structure to withstand the weight of debris or collapses that may occur in the event of a fire. By incorporating Dineen Fire Bricks into their projects, architects and engineers can provide an additional layer of reassurance to the occupants, ensuring their safety during unforeseen emergencies.Versatility and Adaptability:Dineen Fire Bricks cater to the diverse needs of the construction industry by offering a range of product variations. From standard fire-resistant bricks to lightweight options, the company provides solutions suitable for different applications. This versatility allows architects and builders to utilize these bricks in both new construction projects and renovation endeavors. Additionally, Dineen Fire Bricks can be seamlessly integrated with existing building materials, making them an attractive choice for retrofitting older structures.Eco-Friendly Solution:With growing concerns about environmental sustainability, Dineen Fire Bricks embody the company's commitment to developing eco-friendly solutions. These bricks are manufactured using responsibly sourced materials and employ energy-efficient production techniques, minimizing carbon emissions. By opting for Dineen Fire Bricks, construction professionals can contribute to the construction industry's efforts to reduce its ecological footprint, making it a compelling choice for environmentally-conscious builders.Looking Ahead:As the demand for safe and reliable building materials continues to rise, Dineen Fire Bricks are poised to carve out a significant presence in the construction market. With their unmatched fire-resistant capabilities, enhanced structural integrity, versatility, and eco-friendly focus, these bricks are set to redefine construction safety standards. The adoption of Dineen Fire Bricks will undoubtedly revolutionize the way structures are built, ensuring the protection and security of occupants for years to come.Conclusion:Dineen Fire Bricks, with their unrivaled fire resistance, superior structural characteristics, and adaptability, represent a landmark innovation in the construction industry. These revolutionary bricks offer a solution that not only enhances safety but also aligns with sustainable practices. By prioritizing and investing in the use of Dineen Fire Bricks, construction professionals can fulfill their responsibility of safeguarding lives and ensuring robust structures in an ever-evolving world.
Exceptional Quality Magnesia Carbon Brick for a Better Ladle Performance
Magnesia Carbon Brick for Ladle: A Revolutionary Solution for High-Temperature ApplicationsIn the ever-evolving field of refractories, a remarkable development has taken place with the introduction of Magnesia Carbon Brick for Ladle. This groundbreaking product has emerged as a game-changer in high-temperature applications, offering unparalleled performance and durability. With its unique composition and superior properties, this advanced refractory material ensures optimal performance in various industrial processes.Before delving into the specifics of this groundbreaking innovation, let us acquaint ourselves with the company behind this remarkable product. Founded several decades ago, this refractory manufacturer has been at the forefront of delivering cutting-edge solutions to industries worldwide. Known for their commitment to research and development, the company has garnered a reputation for producing best-in-class materials that cater to the most demanding customer requirements.Magnesia Carbon Brick for Ladle, the latest addition to their extensive product portfolio, is engineered to withstand extreme conditions encountered in ladle applications. Ladles are indispensable tools in the steel and metallurgy industries, used for transporting and pouring molten metal. Given the harsh and corrosive nature of these processes, the linings of ladles are subjected to extreme temperatures, chemical reactions, and mechanical stress.Traditionally, bricks made of magnesia and carbon have been used in ladle linings due to their excellent resistance to high temperatures. However, these conventional bricks have limitations such as high oxidation rates, poor thermal shock resistance, and susceptibility to carbon pickup. Recognizing the need for a more robust and reliable solution, our innovators have developed the Magnesia Carbon Brick for Ladle.This advanced refractory material features a unique combination of magnesia, graphite, and various additives, resulting in a high-performance composite with exceptional properties. The addition of graphite enhances the material's thermal shock resistance and provides increased resistance to slag penetration, while the carefully selected additives improve the overall mechanical strength and oxidation resistance.The Magnesia Carbon Brick for Ladle offers several notable advantages over its predecessors. The improved oxidation resistance significantly extends the service life of the lining, reducing downtime and maintenance costs. Moreover, the enhanced thermal shock resistance ensures reliable performance even in rapid temperature fluctuations, minimizing the risk of premature failure.Another key aspect of this revolutionary product is its excellent resistance to carbon pickup. Carbon pickup refers to the absorption of carbon by molten metal, resulting in the formation of carbides and compromising the quality of the final product. By mitigating this issue, the Magnesia Carbon Brick for Ladle ensures the production of high-quality steel with consistent properties.Furthermore, this magnesia carbon brick offers superior corrosion resistance to chemical attacks from molten metals and slags. This resistance is crucial for maintaining the integrity of the ladle lining, preventing leaks or contamination that could impact the overall process efficiency and product quality.Considering the widespread applications of ladles in the steel and metallurgy industries, the adoption of Magnesia Carbon Brick for Ladle is expected to have a significant impact. The extended service life and enhanced performance of this refractory material will help manufacturers optimize their processes, reduce production costs, and improve overall productivity.In conclusion, the introduction of Magnesia Carbon Brick for Ladle marks a significant advancement in the field of refractories. With its remarkable properties and exceptional performance, this innovative product ensures optimal performance in high-temperature applications, such as ladle linings. Developed by a renowned refractory manufacturer, this advanced material underscores their commitment to delivering cutting-edge solutions that meet the evolving needs of industries worldwide. As its adoption grows, this revolutionary brick holds the promise of revolutionizing ladle applications and contributing to the growth and efficiency of various industrial processes.
Discover the Value of High-Quality Alumina Refractory Bricks: A Complete Guide
High-Quality Alumina Refractory Bricks Revolutionize the Construction IndustryThe construction industry is constantly evolving to meet the needs of modern society, and one crucial aspect of ensuring the longevity and safety of structures is the use of high-quality building materials. Alumina refractory bricks have emerged as a game-changer in this field, offering exceptional reliability and durability. This article will delve into the remarkable properties of these bricks and explore why they have become synonymous with excellence in the construction industry.{Company Introduction}In recent years, construction companies worldwide have recognized the importance of using high-quality materials to ensure the safety and stability of buildings. Alumina refractory bricks have quickly become the preferred choice for many construction projects due to their ability to withstand high temperatures and resist corrosion. With their exceptional mechanical strength and insulation properties, these bricks have transformed the way buildings are constructed.One of the key factors contributing to the success of alumina refractory bricks is their composition. These bricks are primarily made of alumina, a mineral known for its remarkable heat resistance. Alumina is combined with other additives and undergoes a precise manufacturing process to create bricks that are exceptionally strong and versatile. The precise composition of alumina refractory bricks allows them to resist the corrosive effects of acids, gases, and high temperatures, ensuring the longevity of structures even in the harshest environments.The superior durability of alumina refractory bricks makes them the ideal choice for a wide range of applications. These bricks are commonly used in industries such as steelmaking, cement manufacturing, and glass production, where high temperatures are prevalent. Their excellent thermal insulation properties minimize heat loss, improving energy efficiency and reducing operational costs.Additionally, the use of alumina refractory bricks enhances the safety of structures. Their ability to withstand extreme temperatures without deformation or crumbling ensures the integrity of buildings, particularly in areas prone to fires or explosions. The exceptional thermal shock resistance of these bricks prevents cracks or fractures when exposed to rapid temperature changes, further enhancing their reliability and safety.Moreover, the versatility of alumina refractory bricks allows architects and engineers to unleash their creativity. With these bricks, complex architectural designs and innovative construction techniques can be realized without compromising the structural integrity of the building. The ability of these bricks to conform to various shapes and sizes makes them an indispensable tool in the hands of construction professionals.{Company Name}, a renowned manufacturer of alumina refractory bricks, has been at the forefront of revolutionizing the construction industry. With over {X} years of experience, they have established themselves as a trusted provider of high-quality building materials. Their commitment to innovation and continuous improvement ensures that their customers have access to the most advanced alumina refractory bricks on the market.{Company Name} prides itself on its state-of-the-art manufacturing facilities, where cutting-edge technology is employed to produce alumina refractory bricks of unmatched quality. These bricks undergo stringent quality control measures to guarantee their reliability and durability. The company also boasts a team of highly skilled technicians and engineers who work tirelessly to develop new formulations and designs, pushing the boundaries of the industry.In conclusion, high-quality alumina refractory bricks have revolutionized the construction industry by offering exceptional durability, reliability, and versatility. Their ability to withstand high temperatures, resist corrosion, and provide excellent thermal insulation has made them the material of choice for numerous construction projects worldwide. Companies like {Company Name} have played a crucial role in advancing the field by manufacturing top-tier alumina refractory bricks. As the construction industry continues to evolve, these bricks will undoubtedly remain an essential component, ensuring the safety and longevity of buildings for generations to come.
Experiencing the Benefits of Alkali Resistant Bricks: Strong and Durable Solution for Industrial Needs
[Publication Name][Date]Alkali Resistant Bricks: An Innovative Solution for High Durability Construction[City], [State] - In a constant endeavor to offer cutting-edge solutions to the construction industry, [Company Name] has launched its new line of Alkali Resistant Bricks. These bricks, specially formulated with advanced technology, boast unparalleled durability and resistance against alkali attacks. With this latest addition to their extensive product portfolio, [Company Name] reinforces its commitment to providing high-quality construction materials to cater to diverse project requirements.The high durability of Alkali Resistant Bricks makes them ideally suited for construction projects where exposure to alkalis is a concern. The advanced formulation ensures these bricks can withstand the corrosive effects that arise from the presence of alkalis in construction materials or the surrounding environment. This exceptional resistance makes Alkali Resistant Bricks an essential choice for applications such as chimneys, incinerators, kilns, and foundations in areas with high alkali content."The launch of our Alkali Resistant Bricks is a significant milestone for us. We firmly believe that this new product will revolutionize the construction industry, offering our clients a reliable solution that can withstand challenging environments," said [Spokesperson Name], spokesperson for [Company Name]. "Our team of experts conducted extensive research and development to ensure that these bricks not only possess exceptional resistance to alkali attacks but also meet the highest standards in terms of durability and reliability."Uniquely designed to resist alkalis, these bricks provide a long-lasting solution for high-alkali environments without compromising on quality or performance. They are manufactured using premium raw materials, carefully selected for their alkali-resistant properties, and go through a rigorous quality control process to ensure consistent, reliable, and defect-free products.Furthermore, Alkali Resistant Bricks offer excellent thermal shock resistance, maintaining structural integrity even in environments with extreme temperature variations. This feature makes them suitable for applications subjected to rapid heating and cooling cycles.The impact of alkali attacks on construction materials is a significant concern for engineers and builders alike. Alkalis, commonly present in cement and other building materials, react with certain minerals in bricks, causing them to degrade over time. This degradation not only weakens the structural integrity of the construction but also affects its aesthetics. The use of Alkali Resistant Bricks addresses these concerns and eliminates the need for frequent repairs or replacements, saving both time and money.As a leader in the construction industry, [Company Name] is dedicated to continuously expanding its product range to meet evolving market demands. Through extensive research and innovation, the company has earned a reputable track record of delivering premium construction materials backed by comprehensive technical support. With the introduction of Alkali Resistant Bricks, [Company Name] aims to set a new industry benchmark while solidifying its position as a reliable partner for construction projects of all scales and complexities.About [Company Name]:[Company Name], a renowned name in the construction sector, has been providing innovative solutions to the industry for over [number] years. With a focus on excellence and sustainability, the company offers a wide range of construction materials, including bricks, cement, concrete additives, and more. [Company Name] collaborates with architects, engineers, and contractors to meet their specific project needs, ensuring high-quality and reliable solutions that stand the test of time.For media inquiries, please contact:[Contact Name][Position][Company Name][Phone][Email]Disclaimer: This press release is for informational purposes only. The content does not constitute investment advice or an endorsement of any product, service, or brand. Readers are encouraged to carry out their own research and seek professional advice before making any investment decisions.
All You Need to Know About Monolithic Castable Refractory for High-Temperature Applications
Monolithic Castable Refractory – Revolutionizing the Refractory IndustryIn the world of heavy industries, refractories play a significant role in ensuring the longevity of high-temperature equipment. Refractories are inorganic, non-metallic materials that can withstand extreme temperatures and harsh environments. They are used as insulators for furnaces, kilns, incinerators, and reactors. Refractories are also used as lining materials in industries such as cement, steel, aluminum, and petrochemical.However, traditional refractory materials such as bricks, tiles, and precast shapes have certain limitations. These materials are time-consuming and require skilled labor for installation. They also have low thermal shock resistance and exhibit cracking, spalling, and erosion after a short period. This leads to frequent maintenance, downtime, and loss of productivity.To overcome these challenges, manufacturers have developed new types of refractory materials, including monolithic castable refractory. This is a revolutionary material that has completely transformed the refractory industry. In this news article, we will explore the benefits and advancements of this innovative material and its impact on various industries.What is Monolithic Castable Refractory?Monolithic castable refractory is a type of refractory material that is made by combining various raw materials such as fine grain, coarse grain, bonding agents, and additives. The mixture is then placed into a mold or sprayed onto a surface. It hardens when exposed to high temperatures and forms a monolithic, seamless structure. The term “monolithic” refers to the fact that it is a single piece, as opposed to traditional refractory materials that are made of multiple pieces.This type of refractory material offers numerous advantages over traditional materials. They include:Less Labor Intensive – Monolithic castables are easier to install compared to traditional materials. They can be poured, sprayed or troweled into place, reducing the need for skilled labor. This significantly lowers the cost of installation and maintenance.Better Insulation Properties - Monolithic castables offer better insulation than traditional materials. This is because they have fewer joints and cracks, which reduce heat loss. This translates to lower energy costs and improved thermal efficiency.Higher Thermal Shock Resistance – Monolithic castables have high thermal shock resistance, which means that they can withstand rapid temperature changes without cracking or spalling. This prolongs the lifespan of the material, reduces maintenance costs and minimizes downtime.Wide Range of Applications – Monolithic castables have a wide range of applications in various industries. They are used as linings in furnaces, kilns, incinerators, and reactors. They are also used as insulating materials for pipes, ducts, boilers, chimneys, and stacks. Their versatility makes them suitable for a broad range of applications.Company Introduction{Remove Brand Name} is a leading global manufacturer of monolithic castable refractory materials. The company was founded over 70 years ago and has since then grown into a global leader in the refractories industry. {Remove Brand Name} offers a wide range of refractory solutions to various industries, including steel, cement, power generation, petrochemical, and aluminum.{Remove Brand Name} has a team of experienced scientists and engineers who are dedicated to developing innovative, high-quality products that meet the needs of their clients. They use state-of-the-art manufacturing processes and equipment to ensure that their products are of the highest quality.{Remove Brand Name} has a strong commitment to sustainable practices, which is reflected in their use of eco-friendly, sustainable raw materials, and their focus on reducing waste and emissions. They work closely with clients to identify their needs and provide customized solutions that meet their specific requirements.Recent DevelopmentsIn recent years, {Remove Brand Name} has made significant advancements in the development of monolithic castable refractory materials. They have developed new products that offer even better thermal performance, insulation, and durability.One of their recent innovations is the use of advanced nanotechnology in their refractory materials. This technology involves the use of nanoparticles that are dispersed throughout the material. The nanoparticles enhance the material's thermal properties, such as thermal conductivity, radiation absorption, and insulation. This results in better thermal efficiency, reduced energy costs, and improved overall performance.{Remove Brand Name} has also developed new manufacturing processes that reduce the environmental impact of their products. They use renewable, eco-friendly raw materials, and reduce waste and emissions during the manufacturing process. This ensures that their products are both high-quality and sustainable.ConclusionIn conclusion, monolithic castable refractory materials have revolutionized the refractory industry. They offer numerous advantages over traditional materials, such as reduced labor costs, better insulation, and higher thermal shock resistance. {Remove Brand Name} is a leading manufacturer of high-quality monolithic castable refractory materials. They have made significant advancements in the development of new products that offer even better thermal performance and durability. With their strong commitment to sustainable practices and client-focused approach, {Remove Brand Name} is poised to continue leading the way in the refractory industry.
Understanding the Basics of Arc Furnace Electrodes
XYZ Corp, a renowned leader in the manufacturing of specialized industrial equipment, has recently developed a groundbreaking product that is set to revolutionize the steel industry. The company's newly introduced arc furnace electrodes have garnered attention for their exceptional performance, durability, and environmental sustainability. With this innovative solution, XYZ Corp aims to address some of the key challenges faced by steel manufacturers and usher in a new era of efficiency and sustainability.Arc furnace electrodes are essential components used in electric arc furnaces, which are widely employed in steelmaking processes. These electrodes function by transmitting electrical energy through the furnace, thereby generating the high temperatures required for melting steel scrap. Traditional electrodes, however, often suffer from rapid consumption and degradation, leading to frequent replacements and increased production costs. Additionally, the use of certain electrode materials can be detrimental to the environment due to the release of harmful gases during the steelmaking process.Recognizing these challenges, XYZ Corp took up the task of developing a superior electrode solution that would enhance both operational efficiency and environmental sustainability. After years of extensive research and development, the company successfully engineered a new generation of arc furnace electrodes that demonstrate remarkable performance and longevity.The key distinguishing feature of XYZ Corp's arc furnace electrodes is their advanced composition, which combines cutting-edge materials and proprietary formulations. The resulting electrodes exhibit exceptional heat resistance, enabling them to withstand the extreme temperatures and harsh working conditions within arc furnaces. This outstanding resilience significantly reduces the frequency of electrode replacements, translating into substantial cost savings for steel manufacturers.Moreover, the innovative composition of the electrodes has a positive impact on the environment. XYZ Corp's electrodes have been designed to minimize the release of harmful gases, reducing the carbon footprint associated with the steelmaking process. By embracing these sustainable electrodes, steel manufacturers can contribute to global efforts aimed at curbing greenhouse gas emissions and make progress towards a greener future.Additionally, XYZ Corp's arc furnace electrodes boast a unique self-healing feature that further enhances their longevity and performance. Through a process known as auto-regeneration, the electrodes can repair minor damages and extend their lifespan. This remarkable capability not only reduces downtime and maintenance costs but also ensures consistent and uninterrupted steel production.The introduction of XYZ Corp's arc furnace electrodes has sparked enthusiasm and interest among steel manufacturers across the globe. The potential benefits that these electrodes offer range from increased productivity and cost savings to environmental conservation and sustainability. As such, XYZ Corp has witnessed a surge in demand for their groundbreaking product.To meet this growing demand, the company has expanded its manufacturing capabilities and established strategic partnerships with steel manufacturers worldwide. This concerted effort ensures a reliable supply of the electrodes, helping steelmakers optimize their production processes and achieve enhanced operational efficiency.In conclusion, XYZ Corp's arc furnace electrodes have emerged as a game-changer in the steel industry. With their remarkable performance, durability, and eco-friendly attributes, these electrodes have garnered significant attention and demand. Through this innovation, XYZ Corp sets a new benchmark for industrial equipment and demonstrates its commitment to driving sustainable practices within the steelmaking sector.
Discover the Benefits of High Liquidity Refractory Castable for Enhanced Performance
High Liquidity Refractory Castable: Revolutionizing Refractory Industry Refractory materials play a crucial role in industries like steel, cement, glass, and petrochemicals. These materials are designed to withstand high temperatures, extreme pressures, and harsh chemical environments. However, not all refractory castables are created equal. Some exhibit low flowability, which can hinder their application and require extensive manpower. Enter the high liquidity refractory castable, a game-changer in the industry. One prominent player in this field, (brand name removed), has developed an innovative high liquidity refractory castable that is transforming the way industries approach refractory lining applications. This groundbreaking product offers unmatched flowability, ease of installation, and exceptional durability. Let's explore the benefits of this advanced castable and the company behind its success.The high liquidity refractory castable by (brand name removed) is made using a proprietary blend of carefully selected raw materials. These materials are finely ground and mixed with an optimized water binder system, resulting in a castable with exceptional flowability. This unique property allows for seamless installation, even in complex shapes and configurations, reducing the need for skilled labor and saving valuable time during construction.One key advantage of this castable is its versatility. It can be used for various refractory lining applications, such as furnace linings, chimneys, kilns, and ladles. Its high liquidity ensures full coverage and precise filling, minimizing gaps and weak points in the lining, which ultimately leads to improved thermal efficiency and superior performance.In addition to its exceptional flowability, the high liquidity refractory castable also exhibits exceptional durability. It has excellent resistance to thermal shocks, chemical attacks, and abrasion, making it ideal for applications exposed to extreme temperatures and corrosive environments. This durability translates into reduced maintenance costs and extended service life, resulting in significant savings for industries.The success of (brand name removed) and its high liquidity refractory castable can be attributed to the company's commitment to research and development. The brand invests heavily in state-of-the-art facilities and a team of highly skilled experts to ensure continuous innovation and improvement of their products. Their rigorous testing procedures and quality control measures ensure that every batch of castable meets the highest industry standards.Furthermore, the company's customer-centric approach sets them apart from their competitors. They work closely with their clients to understand their specific refractory requirements, provide tailored solutions, and offer technical support throughout the installation process. This approach has earned them a solid reputation and a loyal customer base.Looking ahead, (brand name removed) aims to expand its market presence globally by forming strategic partnerships and collaborations. Their goal is to make their high liquidity refractory castable widely available to industries around the world, enabling them to achieve the highest levels of efficiency and productivity.In conclusion, the introduction of high liquidity refractory castable has revolutionized the refractory industry. The innovative product developed by (brand name removed) offers unmatched flowability, ease of installation, and exceptional durability. It has the potential to significantly improve the efficiency and performance of various industries. With their commitment to research and development, along with their customer-centric approach, (brand name removed) is set to lead the refractory industry into a new era of excellence.
Revolutionary Brick Technology Discovered: The Fiery Bubble that Changes Construction Forever
Title: Revolutionary Fire-Resistant Brick Reinvents Building Safety StandardsArticle:In a groundbreaking development in the field of construction and building safety, a new fire-resistant brick has emerged that promises to revolutionize the industry. Developed by a pioneering company in the sector, this innovative product, known as the Fire Bubble Brick (name changed), has already garnered significant attention for its ability to withstand intense heat and protect structures against fire hazards.The Fire Bubble Brick, created by {Company Name}, represents a turning point in building safety, offering a unique solution to the age-old problem of fire-related incidents and their devastating consequences. Engineered to withstand temperatures reaching up to 3000 degrees Celsius, this extraordinary brick provides an exceptional level of protection for various types of buildings, ranging from residential homes to commercial complexes.The secret behind the Fire Bubble Brick's exceptional fire resistance lies in its groundbreaking composition. Constructed using a combination of state-of-the-art ceramic materials and advanced insulation techniques, this brick forms a robust barrier against the spread of fire. By efficiently blocking heat and preventing the transfer of flames, it serves as an impenetrable shield during fire incidents, granting occupants and emergency services crucial time to evacuate and mitigate potential damage.Furthermore, the Fire Bubble Brick is designed to act as an insulator, effectively minimizing heat transfer in both directions. This dual functionality not only reinforces the safety of the building but also serves as a long-term energy-efficient solution.Additionally, this remarkable fire-resistant brick is manufactured using sustainable materials and eco-friendly processes, aligning with the growing global focus on environmental consciousness. By adopting such an approach, {Company Name} showcases its commitment to creating products that meet the demands of a sustainable future without compromising on quality and safety.The versatile nature of the Fire Bubble Brick allows for its application in various construction scenarios. Its lightweight design ensures ease of installation without compromising on its exceptional strength and durability. From constructing fire-resistant walls, floors, and ceilings to creating fire-safe compartments within buildings, this innovative brick serves as an all-encompassing solution for architects, contractors, and building owners.Beyond its already impressive attributes, the Fire Bubble Brick also possesses significant soundproofing properties. With its dense composition, it successfully absorbs and reduces noise transmission, contributing to the overall comfort and well-being of occupants.{Company Name} is a trailblazer in the field of fire-resistant building materials, continuously pushing the boundaries of innovation to provide cutting-edge solutions for the construction industry. With a team of talented engineers and researchers dedicated to developing state-of-the-art products, the company has consistently proven its commitment to building safety.The Fire Bubble Brick represents just one example of {Company Name}'s dedication to revolutionizing the construction industry. By combining advanced technology, exceptional fire resistance, and environmental stewardship, {Company Name} aims to enhance building safety standards and protect lives, structures, and investments.In conclusion, the introduction of the Fire Bubble Brick marks a significant milestone in the pursuit of fire-resistant building materials. This extraordinary product, developed by {Company Name}, offers unparalleled protection against fire hazards while incorporating sustainability and energy efficiency. With its versatility and robustness, the Fire Bubble Brick sets a new benchmark in building safety, ensuring a safer and more secure future for structures and occupants alike.
Demand for High-Quality Carbon Bricks Surges Amidst Growing Industrial Needs
Magnesia Carbon Brick Boosting Production Efficiency for Steel ManufacturingSteel manufacturing has been at the forefront of technological advances and innovation. Manufacturers are always looking for new ways to improve production efficiency, increase product quality, and reduce operating costs. A vital component of the steel manufacturing process is the refractory materials used in the construction of blast furnaces, ladles, and other high-temperature equipment. The quality and durability of these materials are essential for ensuring long-lasting and efficient operation.One of the most popular refractory materials used in the steel industry is Magnesia Carbon Brick. This material is a combination of high purity magnesia and high-quality graphite, allowing for superior thermal shock resistance and corrosion resistance compared to other refractory materials. Magnesia Carbon Brick has been widely applied in the casthouse areas such as the slag line, hot metal transportation chute, and taphole and ladle applications.As the leading refractory manufacturer in China, the {} company has been committed to providing high-quality and reliable refractory solutions to the steel industry for more than 20 years. They have recently launched a new production line for Magnesia Carbon Brick, significantly increasing their production capacity for this highly sought-after product.Magnesia Carbon Brick is preferred by the steel industry for several reasons. Firstly, it is a cost-effective material, with a competitive price when compared to other types of refractories. Secondly, it has a longer lifespan compared to other refractory materials, resulting in lower maintenance costs and a reduction in the frequency of equipment replacement.Thirdly, Magnesia Carbon Brick offers superior thermal shock resistance, which means it can withstand rapid temperature changes without cracking or breaking, prolonging the life of the refractory lining. Finally, Magnesia Carbon Brick has a high resistance to alkaline slag and can resist the erosion caused by molten iron and steel, which is critical to the long-term performance of the refractory lining.These features of Magnesia Carbon Brick are particularly important in the steelmaking process. High-quality refractory materials are necessary to withstand the extreme temperatures and harsh conditions of the blast furnace and other key components of the steelmaking process. Magnesia Carbon Brick can provide the reliability and durability required to operate these critical parts efficiently and cost-effectively.The new Magnesia Carbon Brick production line from {} company is an important development for the steel industry. It provides an opportunity for steel manufacturers to access high-quality refractory materials at competitive prices, helping them to improve production efficiency and reduce operating costs. Additionally, the increased production capacity of {} company means that customers can have a more stable and reliable supply of Magnesia Carbon Brick, ensuring that their operations will not be disrupted by shortages or delays in delivery.The production process of the Magnesia Carbon Brick at {} company is strictly controlled to ensure that the final product is of the highest quality and meets the specific requirements of each individual customer. They use high-purity magnesia and high-quality graphite as raw materials and apply advanced manufacturing techniques, such as mixing, molding, and baking. Additionally, the finished products undergo rigorous testing to ensure that they meet the necessary standards for use in the steel industry.{} company has established a reputation for producing high-quality refractory products and providing excellent customer service. They have a team of experienced engineers and technicians who work closely with customers to provide customized refractory solutions tailored to meet their individual needs. Whether it's choosing the right materials or providing on-site technical support, {} company is committed to ensuring their customers' success.In conclusion, the steel industry is highly competitive, and manufacturers are always searching for ways to improve their production efficiency and reduce operating costs. The Magnesia Carbon Brick produced by {} company is a cost-effective, durable, and reliable refractory material that can help steel manufacturers achieve these goals. With their new and expanded production facilities, {} company is poised to become a leading supplier of Magnesia Carbon Brick to the steel industry.
Discover the Benefits and Uses of High Alumina Insulation Bricks
High Alumina Insulation Bricks Showcase Exceptional Quality and Unmatched Insulation Properties[City, Date] – In a groundbreaking announcement, renowned brick manufacturing company [Company Name] has introduced a revolutionary product – high alumina insulation bricks – that are set to redefine the industry standards. With its exceptional quality and unmatched insulation properties, these bricks are poised to take the construction and insulation sectors by storm.Made from a unique blend of high-quality alumina, these insulation bricks are designed to provide superior thermal efficiency and insulation. With ever-increasing energy costs and a growing global focus on sustainability, optimizing insulation is paramount for both residential and commercial buildings. These new high alumina insulation bricks offer a promising solution.Compared to traditional bricks, [Company Name]'s high alumina insulation bricks possess the distinct advantage of significantly reducing heat transfer. The innovative manufacturing process involves carefully selecting and processing raw materials to create a product with superior insulation properties. This results in lower energy consumption, increased energy efficiency, and reduced dependence on artificial heating or cooling systems.One of the key reasons behind the exceptional insulation capabilities of these bricks is their high alumina content. Alumina is a compound known for its remarkable resistance to heat and its excellent insulation properties. By incorporating a relatively higher percentage of alumina while manufacturing these bricks, [Company Name] has achieved a remarkable thermal efficiency that surpasses industry standards.Furthermore, [Company Name] ensures that the manufacturing process adheres to stringent quality control measures. Rigorous tests and inspections are conducted at various stages, ensuring that each brick meets the highest quality standards. This meticulous attention to detail guarantees that customers receive a reliable, power-saving, and durable insulation solution that meets their specific requirements.The high alumina insulation bricks offered by [Company Name] are available in a range of sizes and shapes, making them suitable for various construction applications. Whether it's the construction of furnaces, stoves, kilns, or any other high-temperature environment, these bricks exhibit exceptional performance and resistance to thermal shock.Additionally, [Company Name] prides itself on its commitment to sustainable practices. The manufacturing process for the high alumina insulation bricks is designed to minimize waste and reduce environmental impact. By utilizing advanced technology and efficient recycling methods, the company ensures that its operations are conducted with minimal carbon footprints, promoting a healthier and greener planet.[Company Name] has a rich history in the brick manufacturing industry, boasting years of experience and expertise. With a team of skilled professionals and cutting-edge facilities, the company has consistently delivered products of exceptional quality and performance. The introduction of high alumina insulation bricks further cements their position as an industry leader and their dedication to innovation.As the demand for energy-efficient and sustainable construction materials grows, [Company Name] remains at the forefront of the industry, continually striving to provide groundbreaking solutions. The high alumina insulation bricks are a testament to their dedication to customer satisfaction and their commitment to shaping the future of the construction industry.About [Company Name]:[Company Name] is a renowned brick manufacturing company with years of experience in the industry. Known for their commitment to quality and innovation, they consistently deliver products that exceed customer expectations. With a focus on energy efficiency and sustainability, [Company Name] aims to revolutionize the construction industry with their exceptional high alumina insulation bricks.For media inquiries, please contact:[Contact Name][Company Name][Phone Number][Email Address]