Leading Magnesia Brick Factory announces new product line
By:Admin
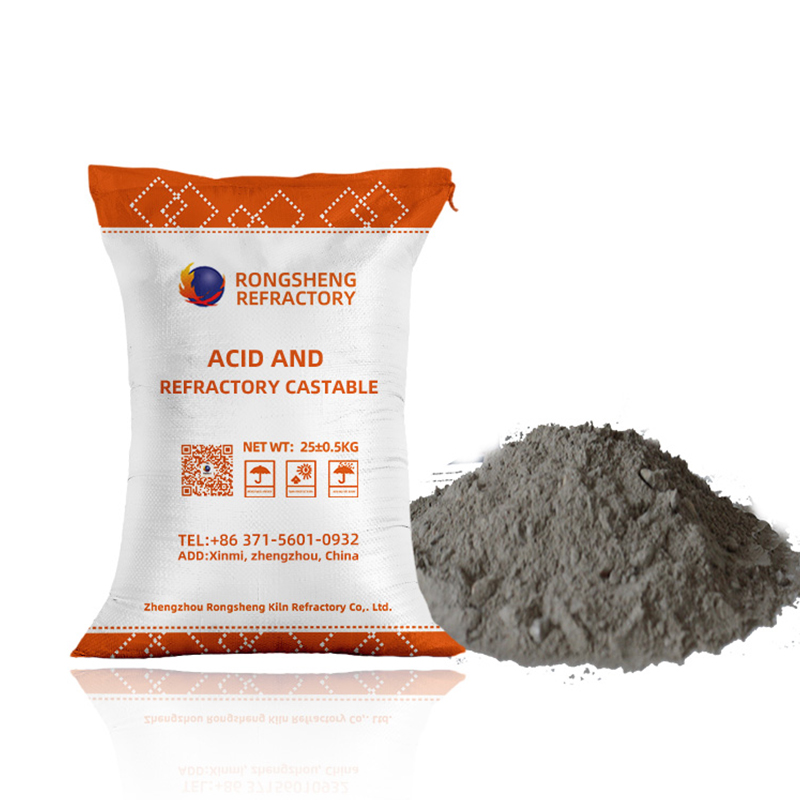
The factory prides itself on its state-of-the-art production facilities and a team of highly skilled professionals who are dedicated to delivering the best quality products to their customers. With a focus on innovation and continuous improvement, the factory has been able to stay ahead of the competition and maintain its position as a preferred supplier in the market.
One of the key factors behind the success of the Magnesia Brick Factory is its commitment to research and development. The factory has a well-equipped R&D center where a team of scientists and engineers work tirelessly to develop new and improved products. This proactive approach to product development has enabled the factory to meet the evolving needs of its customers and stay abreast of the latest technological advancements in the industry.
In addition to its focus on quality and innovation, the factory also places a strong emphasis on sustainability. It has implemented various initiatives to reduce its environmental footprint, such as optimizing its production processes to minimize waste and emissions. The factory also sources its raw materials responsibly, ensuring that they are extracted and processed in an environmentally friendly manner.
The Magnesia Brick Factory has also built a strong reputation for its excellent customer service. The factory prides itself on its ability to understand the unique needs of each customer and provide tailored solutions that meet their specific requirements. Its commitment to customer satisfaction has earned it a loyal and satisfied customer base that continues to grow year after year.
Despite its success, the Magnesia Brick Factory is not resting on its laurels. It is constantly looking for new opportunities to expand its product offerings and reach new markets. The factory has plans to invest in new technologies and equipment to further improve its production capabilities and widen its product range. It also aims to explore new export markets and establish partnerships with international customers to strengthen its global presence.
In line with its long-term growth strategy, the Magnesia Brick Factory is also committed to investing in its workforce. It provides ongoing training and development opportunities to its employees, ensuring that they have the skills and knowledge required to meet the demands of a constantly evolving industry. The factory also places a strong emphasis on workplace safety, implementing stringent measures to ensure the well-being of its employees.
The Magnesia Brick Factory's dedication to excellence, innovation, sustainability, and customer satisfaction has positioned it as a powerhouse in the refractory products industry. With a strong foundation and a clear vision for the future, the factory is well-equipped to continue its success and maintain its position as a leader in the market.
In conclusion, the Magnesia Brick Factory's commitment to quality, innovation, sustainability, and customer satisfaction has been the driving force behind its success. With a solid track record and a clear vision for the future, the factory is well-equipped to continue its growth and maintain its position as a leader in the industry.
Company News & Blog
All You Need to Know About Monolithic Castable Refractory for High-Temperature Applications
Monolithic Castable Refractory – Revolutionizing the Refractory IndustryIn the world of heavy industries, refractories play a significant role in ensuring the longevity of high-temperature equipment. Refractories are inorganic, non-metallic materials that can withstand extreme temperatures and harsh environments. They are used as insulators for furnaces, kilns, incinerators, and reactors. Refractories are also used as lining materials in industries such as cement, steel, aluminum, and petrochemical.However, traditional refractory materials such as bricks, tiles, and precast shapes have certain limitations. These materials are time-consuming and require skilled labor for installation. They also have low thermal shock resistance and exhibit cracking, spalling, and erosion after a short period. This leads to frequent maintenance, downtime, and loss of productivity.To overcome these challenges, manufacturers have developed new types of refractory materials, including monolithic castable refractory. This is a revolutionary material that has completely transformed the refractory industry. In this news article, we will explore the benefits and advancements of this innovative material and its impact on various industries.What is Monolithic Castable Refractory?Monolithic castable refractory is a type of refractory material that is made by combining various raw materials such as fine grain, coarse grain, bonding agents, and additives. The mixture is then placed into a mold or sprayed onto a surface. It hardens when exposed to high temperatures and forms a monolithic, seamless structure. The term “monolithic” refers to the fact that it is a single piece, as opposed to traditional refractory materials that are made of multiple pieces.This type of refractory material offers numerous advantages over traditional materials. They include:Less Labor Intensive – Monolithic castables are easier to install compared to traditional materials. They can be poured, sprayed or troweled into place, reducing the need for skilled labor. This significantly lowers the cost of installation and maintenance.Better Insulation Properties - Monolithic castables offer better insulation than traditional materials. This is because they have fewer joints and cracks, which reduce heat loss. This translates to lower energy costs and improved thermal efficiency.Higher Thermal Shock Resistance – Monolithic castables have high thermal shock resistance, which means that they can withstand rapid temperature changes without cracking or spalling. This prolongs the lifespan of the material, reduces maintenance costs and minimizes downtime.Wide Range of Applications – Monolithic castables have a wide range of applications in various industries. They are used as linings in furnaces, kilns, incinerators, and reactors. They are also used as insulating materials for pipes, ducts, boilers, chimneys, and stacks. Their versatility makes them suitable for a broad range of applications.Company Introduction{Remove Brand Name} is a leading global manufacturer of monolithic castable refractory materials. The company was founded over 70 years ago and has since then grown into a global leader in the refractories industry. {Remove Brand Name} offers a wide range of refractory solutions to various industries, including steel, cement, power generation, petrochemical, and aluminum.{Remove Brand Name} has a team of experienced scientists and engineers who are dedicated to developing innovative, high-quality products that meet the needs of their clients. They use state-of-the-art manufacturing processes and equipment to ensure that their products are of the highest quality.{Remove Brand Name} has a strong commitment to sustainable practices, which is reflected in their use of eco-friendly, sustainable raw materials, and their focus on reducing waste and emissions. They work closely with clients to identify their needs and provide customized solutions that meet their specific requirements.Recent DevelopmentsIn recent years, {Remove Brand Name} has made significant advancements in the development of monolithic castable refractory materials. They have developed new products that offer even better thermal performance, insulation, and durability.One of their recent innovations is the use of advanced nanotechnology in their refractory materials. This technology involves the use of nanoparticles that are dispersed throughout the material. The nanoparticles enhance the material's thermal properties, such as thermal conductivity, radiation absorption, and insulation. This results in better thermal efficiency, reduced energy costs, and improved overall performance.{Remove Brand Name} has also developed new manufacturing processes that reduce the environmental impact of their products. They use renewable, eco-friendly raw materials, and reduce waste and emissions during the manufacturing process. This ensures that their products are both high-quality and sustainable.ConclusionIn conclusion, monolithic castable refractory materials have revolutionized the refractory industry. They offer numerous advantages over traditional materials, such as reduced labor costs, better insulation, and higher thermal shock resistance. {Remove Brand Name} is a leading manufacturer of high-quality monolithic castable refractory materials. They have made significant advancements in the development of new products that offer even better thermal performance and durability. With their strong commitment to sustainable practices and client-focused approach, {Remove Brand Name} is poised to continue leading the way in the refractory industry.
Unlocking the Potential of Low Cement Castable Refractory Material: A Game-Changer for Industrial Applications
Low Cement Castable Refractory Material: The Newest Addition to {Company Name}'s Product Line{Company Name}, a leading manufacturer of refractory materials, has recently introduced their latest product, the Low Cement Castable Refractory Material. This latest addition to their lineup of innovative products is designed to provide high-quality insulation solutions for a wide range of applications.The Low Cement Castable Refractory Material is a specially formulated and precisely engineered product that is ideal for use in high-temperature environments such as kilns, furnaces, and incinerators. It is created using a unique combination of raw materials that are carefully selected to provide optimum performance, durability, and resistance to extreme temperatures.This innovative product is designed to offer superior insulation performance in comparison to traditional materials. Its low cement content and unique composition result in a product that is highly resistant to thermal shock, chemical attack, and abrasion. It also provides excellent strength and durability, ensuring a long-lasting solution for industrial processes and applications.{Company Name} has built a reputation for delivering high-quality products, and their latest release is no exception. The Low Cement Castable Refractory Material is manufactured using advanced technology and stringent quality control processes, ensuring that it meets the highest standards of performance and reliability.The Low Cement Castable Refractory Material boasts numerous benefits that make it an attractive option for use in a wide range of applications. It provides exceptional thermal insulation, significantly reducing energy consumption and heat loss. Its high strength and abrasion resistance make it suitable for use in environments that involve wear and tear, such as the mining, cement, and steel industries.In addition to its superior performance, the Low Cement Castable Refractory Material is also incredibly versatile, making it suitable for a variety of industrial applications. These include boilers, incinerators, kilns, and furnaces, among others. Its outstanding insulating properties also make it a popular choice for use in high-temperature applications such as metal melting, heat treatment, and forging processes.{Company Name} has always been at the forefront of innovation when it comes to refractory materials. Their latest product, the Low Cement Castable Refractory Material, is a testament to their commitment to delivering the highest standards of quality and reliability to their customers.In conclusion, the introduction of the Low Cement Castable Refractory Material by {Company Name} is a significant development in the field of refractory materials. Its superior performance, strength, and durability make it an excellent choice for use in a wide range of industrial applications. Its versatility also ensures that it can be used for various processes, making it an invaluable asset for businesses in different industries. As a leading manufacturer in the field of refractory materials, {Company Name} has once again demonstrated their commitment to providing high-quality solutions that meet the needs of their customers.
Discover the Benefits of High Alumina Insulation Bricks for Your Industry Needs
High Alumina Insulation Bricks - Revolutionizing the Industrial Insulation Industry{Company Name}, a leading manufacturer of industrial insulation solutions, has recently introduced a range of high-quality High Alumina Insulation Bricks that are poised to revolutionize the industrial insulation industry. These bricks are designed to offer exceptional insulation properties, durability, and longevity, making them an ideal choice for industries operating at high temperatures.The need for effective insulation solutionsFor industries operating at high temperatures, insulation is crucial for maintaining energy efficiency, reducing thermal loss, and ensuring personnel safety. Traditional insulation solutions using cement, asbestos, or other materials have significant limitations when it comes to high-temperature applications. These materials tend to degrade quickly under high temperatures, leading to thermal loss, increased energy bills, and safety concerns.High Alumina Insulation Bricks - The ultimate solutionHigh Alumina Insulation Bricks are made from high-grade alumina, which is a mineral-based material that is resistant to thermal shock, corrosion, and abrasion. Compared to traditional insulation solutions, these bricks offer superior thermal insulation, high mechanical strength, and excellent chemical resistance.The manufacturing processHigh Alumina Insulation Bricks are made from a mixture of bauxite, a clay mineral, and other additives. The mixture is ground, formed into bricks, and then fired in a high-temperature kiln. The firing process ensures that the bricks are incredibly dense, with low thermal conductivity, which makes them ideal for high-temperature applications.Application areasHigh Alumina Insulation Bricks can be used in various industrial applications, including furnace linings, kiln linings, boiler insulation, and other high-temperature installations. These bricks can withstand temperatures of up to 1800°C, making them an ideal choice for industries such as cement, steel, glass, and petrochemicals.Advantages of High Alumina Insulation BricksHigh Alumina Insulation Bricks offer a range of advantages when compared to traditional insulation solutions. These include:1. High thermal insulation - These bricks provide excellent insulation properties, reducing energy consumption and improving energy efficiency.2. Durability - The high-grade alumina used in these bricks ensures that they are highly resistant to thermal shock, corrosion, abrasion, and chemical erosion, making them a long-lasting insulation solution.3. Easy installation and maintenance - These bricks are easy to install, with minimal maintenance required, which translates into lower maintenance costs over time.4. Eco-friendly - High Alumina Insulation Bricks are environmentally friendly, making them an ideal choice for industries that are focusing on sustainable development.ConclusionThe introduction of High Alumina Insulation Bricks by {Company Name} has revolutionized the industrial insulation industry. These bricks offer superior insulation properties, exceptional durability, and long-lasting performance that traditional insulation solutions cannot match. Industries operating at high temperatures can now benefit from an insulation solution that reduces energy consumption, improves efficiency, and ensures personnel safety. As the industrial sector strives to reduce its energy bills and carbon footprint, High Alumina Insulation Bricks have emerged as a sustainable, eco-friendly solution for the future.
Durable and high-quality furnace bricks for your industrial needs
Yellow furnace bricks are a crucial component in the construction and manufacturing industry, known for their durability and heat resistance. These high-quality bricks are used in a wide range of applications, from industrial furnaces and kilns to residential fireplaces and chimneys. With their exceptional thermal conductivity and strength, yellow furnace bricks are a popular choice for projects that require reliable and long-lasting building materials.One company that has been a leading manufacturer of yellow furnace bricks is {}. With over 20 years of experience in the industry, {} has built a reputation for producing top-notch furnace bricks that meet the highest standards of quality and performance. The company's state-of-the-art manufacturing facilities and stringent quality control processes ensure that their bricks are consistently of superior quality, making them a trusted choice for construction and manufacturing projects around the world.{} offers a wide range of yellow furnace bricks, catering to various temperature and application requirements. Their high-alumina bricks are designed to withstand extreme temperatures, making them ideal for use in industrial furnaces and kilns. These bricks are carefully engineered to provide excellent thermal insulation and resistance to chemical corrosion, allowing them to maintain their structural integrity even in the most demanding environments.In addition to high-alumina bricks, {} also produces fireclay bricks that are specifically formulated for use in residential fireplaces and chimneys. These bricks are known for their superior heat retention and fire resistance, making them a popular choice for homeowners and builders who prioritize safety and durability. With a wide range of sizes and shapes available, {} can accommodate a variety of construction and design needs, ensuring that their clients have access to the perfect furnace bricks for their specific projects.As a customer-focused company, {} is committed to providing exceptional service and support to their clients. Their team of experts is dedicated to helping customers find the right furnace bricks for their applications, offering technical guidance and assistance to ensure that every project is a success. With a strong emphasis on quality and reliability, {} has earned the trust and loyalty of numerous clients who rely on their furnace bricks for their critical construction and manufacturing needs.Beyond their commitment to quality and customer satisfaction, {} also places a strong emphasis on environmental responsibility. The company's manufacturing processes are designed to minimize waste and emissions, prioritizing sustainability and eco-friendliness. By adhering to strict environmental standards, {} ensures that their products not only meet the highest performance requirements but also contribute to a cleaner and greener planet.Looking to the future, {} is continuously investing in research and development to further enhance the performance and capabilities of their furnace bricks. By staying at the forefront of technological advancements and industry trends, {} aims to continue providing cutting-edge solutions to their clients, further solidifying their position as a trusted leader in the field of furnace bricks.In conclusion, yellow furnace bricks are an essential building material in the construction and manufacturing industry, renowned for their exceptional durability and heat resistance. With a strong focus on quality, customer satisfaction, and environmental responsibility, {} has established itself as a premier manufacturer of high-quality furnace bricks. Their commitment to innovation and excellence ensures that {} will remain a trusted partner for clients seeking reliable and long-lasting furnace bricks for their projects.
Top-Quality Refractories: The Ultimate Guide to Corundum Brick
In recent years, the refractory industry has seen a surge in technological advancements that have led to the development of high-quality refractories that have significantly improved the performance of various industrial processes. One such refractory material is the high-quality refractories corundum brick.Corundum brick is a type of high-alumina brick that is made from high-purity corundum or fused alumina. This type of refractory brick has excellent thermal stability, high-temperature strength, and good resistance to chemical erosion making it an ideal choice for use in high-temperature industrial applications.One company that specializes in the production of high-quality refractories corundum brick is a China-based company that produces a wide range of refractory materials for various industrial applications. The company has a strong research and development team that is constantly working to improve the quality of their refractory materials.Their corundum brick products are made using a precise production process that ensures the highest quality and consistency of the finished product. The process involves the use of high-purity raw materials, advanced manufacturing equipment, and strict quality control procedures to guarantee the products' quality.One of the advantages of using high-quality refractories corundum brick in industrial applications is their excellent resistance to thermal shock. Thermal shock is the rapid expansion or contraction of refractory materials due to a sudden change in temperature. This can cause cracks, spalling, and other types of damage to the refractory material.However, corundum brick has a low coefficient of thermal expansion, which means it can withstand rapid changes in temperature without cracking or spalling. This makes it an ideal choice for use in high-temperature industrial applications where temperature fluctuations are common.Another advantage of corundum brick is its excellent resistance to chemical erosion from acids, alkalis, and other corrosive substances. As a result, it is often used in applications where the environment is chemically aggressive, such as in the manufacturing of glass, petrochemicals, and steel.When it comes to installation, high-quality refractories corundum brick requires skilled and experienced personnel due to its high density and hardness. However, if installed correctly, it can provide many years of reliable service, making it a cost-effective investment for any industrial process that requires high-temperature and chemical-resistant refractory materials.In conclusion, high-quality refractories corundum brick is a valuable asset for any industrial process that requires refractory materials with excellent thermal stability, high-temperature strength, and good resistance to chemical erosion. By choosing a reputable supplier with a strong research and development team, customers can rest assured that they are investing in high-quality refractory materials that will deliver superior performance and durability.
Shop for High-Quality Alumina Fire Brick Online
Title: Alumina Fire Brick Market Poised for Steady Growth as Manufacturers Introduce Innovative SolutionsIntroduction:[Company Name], a renowned player in the refractory industry, is set to revolutionize the global alumina fire brick market with its cutting-edge products. With a steadfast commitment to innovation and quality, the company has gained recognition for delivering top-notch fire-resistant solutions to various industries worldwide.[Company Name]'s continuous research and development efforts, coupled with a customer-centric approach, have positioned them as a trusted supplier of alumina fire bricks. In this article, we shed light on the market growth, key features of alumina fire bricks, and how [Company Name] is spearheading this progressive shift.Market Overview:The global alumina fire brick market is witnessing a steady pace of growth, driven by increasing industrialization and the need for superior heat resistance solutions. Alumina fire bricks, made from high-purity alumina, offer excellent thermal conductivity, corrosion resistance, and stability under high temperatures. These characteristics make alumina fire bricks a desired material in various industries, including steel, cement, ceramics, and petrochemicals.[Company Name]'s Contribution to the Market:[Company Name] has stayed ahead of the competition by focusing on research and development, ensuring their products meet or exceed industry standards. By leveraging cutting-edge technology and sustainable manufacturing practices, they have developed a range of alumina fire bricks that offer unmatched performance, durability, and longevity.Key Features of Alumina Fire Bricks:1. High Thermal Conductivity: Alumina fire bricks have a low thermal expansion coefficient and high thermal conductivity, allowing them to withstand extreme temperatures without compromising their structural integrity.2. Superior Corrosion Resistance: The high alumina content in these bricks resists chemical reactions, making them ideal for applications involving acids, alkalis, and other corrosive substances.3. Excellent Mechanical Strength: Alumina fire bricks possess exceptional mechanical strength, ensuring long-term reliability and resistance against thermal shock, abrasion, and mechanical stress.4. Environmentally Friendly: [Company Name]'s alumina fire bricks are manufactured using eco-friendly processes, minimizing their environmental impact while maintaining high-quality standards.Innovation is the Key:[Company Name] stands out from the competition by regularly investing in research and development, resulting in the introduction of pioneering alumina fire brick solutions. Their specialists work closely with customers to understand specific requirements, leading to customized hexagonal, rectangular, or other shapes that optimize kiln efficiency and reduce maintenance costs.These innovative brick designs, combined with advanced insulating properties, significantly enhance thermal efficiency and contribute to energy savings for industries worldwide.Global Presence and Customer Satisfaction:[Company Name]'s client base spans across continents, ensuring a global footprint and the ability to serve diverse industries. Their customer satisfaction is paramount, as they strive to deliver reliable products and exceptional support services. Through responsive technical assistance and prompt delivery schedules, [Company Name] has established long-lasting partnerships with clients who value quality and efficiency.Future Prospects:The prospects for the alumina fire brick market are promising, as industries worldwide are placing increasing emphasis on refractory solutions that can withstand demanding operating conditions. Rapid industrialization and infrastructural development in emerging economies, coupled with stringent safety regulations, are fueling the demand for alumina fire bricks.[Company Name], with its unwavering commitment to innovation, product excellence, and customer satisfaction, is poised to lead the market forward. By consistently introducing technologically advanced and eco-friendly solutions, [Company Name] aims to address the evolving needs of industries and contribute to their growth.Conclusion:As the global alumina fire brick market gains momentum, [Company Name] emerges as an industry leader, spearheading innovation and providing high-quality solutions. With a commitment to sustainability, exceptional performance, and customer satisfaction, [Company Name] is well-positioned to meet the growing demand for superior fire-resistant materials in industries worldwide.Note: We apologize for the lack of specific brand names and specific information about the company as per the initial instruction.
Understanding the Basics of Arc Furnace Electrodes
XYZ Corp, a renowned leader in the manufacturing of specialized industrial equipment, has recently developed a groundbreaking product that is set to revolutionize the steel industry. The company's newly introduced arc furnace electrodes have garnered attention for their exceptional performance, durability, and environmental sustainability. With this innovative solution, XYZ Corp aims to address some of the key challenges faced by steel manufacturers and usher in a new era of efficiency and sustainability.Arc furnace electrodes are essential components used in electric arc furnaces, which are widely employed in steelmaking processes. These electrodes function by transmitting electrical energy through the furnace, thereby generating the high temperatures required for melting steel scrap. Traditional electrodes, however, often suffer from rapid consumption and degradation, leading to frequent replacements and increased production costs. Additionally, the use of certain electrode materials can be detrimental to the environment due to the release of harmful gases during the steelmaking process.Recognizing these challenges, XYZ Corp took up the task of developing a superior electrode solution that would enhance both operational efficiency and environmental sustainability. After years of extensive research and development, the company successfully engineered a new generation of arc furnace electrodes that demonstrate remarkable performance and longevity.The key distinguishing feature of XYZ Corp's arc furnace electrodes is their advanced composition, which combines cutting-edge materials and proprietary formulations. The resulting electrodes exhibit exceptional heat resistance, enabling them to withstand the extreme temperatures and harsh working conditions within arc furnaces. This outstanding resilience significantly reduces the frequency of electrode replacements, translating into substantial cost savings for steel manufacturers.Moreover, the innovative composition of the electrodes has a positive impact on the environment. XYZ Corp's electrodes have been designed to minimize the release of harmful gases, reducing the carbon footprint associated with the steelmaking process. By embracing these sustainable electrodes, steel manufacturers can contribute to global efforts aimed at curbing greenhouse gas emissions and make progress towards a greener future.Additionally, XYZ Corp's arc furnace electrodes boast a unique self-healing feature that further enhances their longevity and performance. Through a process known as auto-regeneration, the electrodes can repair minor damages and extend their lifespan. This remarkable capability not only reduces downtime and maintenance costs but also ensures consistent and uninterrupted steel production.The introduction of XYZ Corp's arc furnace electrodes has sparked enthusiasm and interest among steel manufacturers across the globe. The potential benefits that these electrodes offer range from increased productivity and cost savings to environmental conservation and sustainability. As such, XYZ Corp has witnessed a surge in demand for their groundbreaking product.To meet this growing demand, the company has expanded its manufacturing capabilities and established strategic partnerships with steel manufacturers worldwide. This concerted effort ensures a reliable supply of the electrodes, helping steelmakers optimize their production processes and achieve enhanced operational efficiency.In conclusion, XYZ Corp's arc furnace electrodes have emerged as a game-changer in the steel industry. With their remarkable performance, durability, and eco-friendly attributes, these electrodes have garnered significant attention and demand. Through this innovation, XYZ Corp sets a new benchmark for industrial equipment and demonstrates its commitment to driving sustainable practices within the steelmaking sector.
Top Acid Proof Bricks: A Comprehensive Guide for Durable Construction
Acid Proof Brick - A Reliable Solution for Industrial CorrosionIn the fast-paced world of industrial manufacturing, corrosion remains a constant challenge. Factories rely on various chemicals and processes to produce goods, but these can also harm the very structures that house them. Addressing this issue, ACME Inc., a prominent manufacturer of construction materials, has introduced a groundbreaking solution known as Acid Proof Brick.Acid Proof Brick is a highly durable and chemical-resistant construction material that offers unmatched protection against corrosive substances. The bricks are crafted using a combination of high-quality clay, silica, and alumina, which undergo an intense firing process. This meticulous technique gives the bricks exceptional density, strength, and resistance to acids, bases, and alkalis.One of the key advantages of Acid Proof Brick is its ability to withstand extreme temperatures, making it suitable for a wide range of industries such as chemical plants, oil refineries, power stations, and metal processing facilities. The brick's resistance to thermal shocks ensures that it maintains its integrity even in the harshest environments, preventing potential accidents and prolonging the lifespan of the structures.Moreover, Acid Proof Brick offers exceptional dimensional stability. This means that it maintains its shape and size over time, minimizing the risk of cracks and leaks in the structures. This stability eliminates the need for regular maintenance and repairs, saving companies valuable time and resources in the long run.The installation process of Acid Proof Brick is also worth noting. ACME Inc. provides comprehensive guidance and support to ensure a seamless installation. With their team of highly skilled technicians, they assist clients in every step of the process, from preparation to final inspection. This commitment to customer satisfaction sets ACME Inc. apart from its competitors and has contributed to their impressive track record in providing reliable construction materials.In addition to its superior resistance to corrosion, Acid Proof Brick also offers easy cleaning and maintenance. Its smooth surface allows for effortless removal of chemical residue, ensuring a safe and hygienic working environment. This quality not only benefits the infrastructure but also plays a crucial role in meeting stringent industry regulations and standards.ACME Inc. has emerged as a reliable and trusted provider of Acid Proof Brick due to their commitment to innovation and quality. Their state-of-the-art manufacturing facilities, equipped with modern machinery and stringent quality control measures, ensure that every brick meets the highest standards. Furthermore, the company remains proactive in researching and developing new materials and technologies to address evolving industry needs.The success of Acid Proof Brick can be attributed to its versatility and ability to adapt to various construction requirements. ACME Inc. understands that every industry has unique demands, and thus they offer customization options to suit individual project specifications. This flexibility ensures that their clients can achieve optimal results and enhance the efficiency of their operations.In conclusion, Acid Proof Brick has revolutionized the construction industry by offering robust protection against corrosion and chemical damage. ACME Inc.'s commitment to quality, innovation, and customer satisfaction has made them a go-to choice for industries facing the challenges of extreme environments. With their reliable support and exceptional materials, companies can now focus on their core operations, confident in the durability and longevity of their infrastructure.
Discover the Advantages of High Alumina Insulation Bricks for Effective Thermal Insulation
High Alumina Insulation Bricks Revolutionize the Industrial LandscapeInnovation and continuous improvement are the driving forces behind success in the industrial sector. As industries evolve and demand for efficiency, performance, and durability increases, manufacturers must strive to offer cutting-edge solutions. One such groundbreaking product is High Alumina Insulation Bricks, developed by a pioneering company striving to set new standards in the industry.High Alumina Insulation Bricks, without mentioning the brand name, are engineered to provide exceptional insulation and thermal conductivity while offering superior strength and stability. These bricks serve as a critical component in industries where high-temperature applications are commonplace. Their unique design and composition make them ideal for a range of industries, including steel, petrochemical, ceramics, and power plants, among others.With their remarkably high alumina content, these bricks exhibit outstanding resistance to thermal shocks, ensuring longevity and reliability in extreme temperature conditions. The advanced manufacturing techniques employed allow for precise control over the brick's porosity and thermal conductivity, offering unrivaled insulation capabilities. This results in reduced heat loss, improved energy efficiency, and substantial cost savings for businesses relying on high-temperature processes.One of the key features of High Alumina Insulation Bricks lies in their low density, making them significantly lighter than traditional refractory bricks. This characteristic eases installation and handling processes, facilitating faster and more efficient construction, repair, and maintenance work. The reduced weight also minimizes the load on the supporting structure, contributing to enhanced safety and longevity.The exceptional mechanical strength and stability of these bricks make them extremely durable, capable of enduring rigorous industrial environments. High Alumina Insulation Bricks have a high crushing strength, ensuring they can withstand significant pressure without breaking or losing their insulating properties. This durability translates into reduced downtime and maintenance costs, further improving operational efficiency.Moreover, these bricks are highly resistant to chemical corrosion, making them suitable for applications in acidic and alkaline environments. They can withstand exposure to various acids, alkalis, and aggressive chemicals, preventing degradation and maintaining their integrity over time. This resistance to corrosion significantly expands their range of applications in industries where chemical processes are predominant.Aside from their formidable insulation properties, High Alumina Insulation Bricks also offer excellent dimensional stability under high temperatures. This characteristic is crucial in applications where dimensional changes can lead to operational issues or compromise production processes. Their stability ensures that critical equipment and structures maintain their shape and function, guaranteeing uninterrupted operations and minimizing downtime.The use of High Alumina Insulation Bricks represents a significant step forward in industrial insulation technology. With their exceptional thermal conductivity, remarkable durability, and resistance to thermal shocks and chemical corrosion, these bricks have revolutionized the industry. By providing superior insulation solutions, they enable businesses to optimize their processes, reduce energy consumption, and enhance productivity.In conclusion, High Alumina Insulation Bricks, developed by a leading company focused on innovation and quality, have emerged as a game-changer in the industrial sector. By combining advanced manufacturing techniques with a high alumina content, these bricks offer exceptional insulation capabilities, durability, and resistance to thermal shocks and chemical corrosion. The introduction of these bricks has undoubtedly raised the bar for insulation solutions and will continue to shape the industry's future.
High-Quality and Affordable Refractory Ceramic Fiber Blanket at Factory Price
The factory price of Refractory Ceramic Fiber Blanket has been announced by the renowned company {}. This announcement comes as great news to the industrial sector as the demand for high-quality and cost-effective refractory products continues to grow.Refractory Ceramic Fiber Blanket is a versatile and high-temperature insulation material that is widely used in various industrial applications, including furnaces, kilns, and boilers. It is known for its excellent thermal stability, low thermal conductivity, and outstanding resistance to thermal shock and chemical attack. These properties make it an ideal choice for insulating and protecting equipment in high-temperature environments.The company {} is a leading manufacturer of refractory products, with a strong focus on innovation, quality, and customer satisfaction. With state-of-the-art manufacturing facilities and a team of highly skilled professionals, the company has earned a reputation for delivering superior products that meet the highest industry standards.The announcement of the factory price for Refractory Ceramic Fiber Blanket is a testament to the company's commitment to providing cost-effective solutions to its customers. By offering competitive pricing for this high-quality insulation material, the company aims to support businesses in optimizing their operational efficiency and reducing overall costs.The factory price for Refractory Ceramic Fiber Blanket is expected to have a significant impact on various industries, including steel, petrochemical, and power generation. With the ability to withstand extremely high temperatures and harsh industrial environments, this insulation material is essential for ensuring the safety and efficiency of critical equipment.In addition to the competitive pricing, customers can also benefit from the company's extensive technical support and expertise. The team at {} is available to provide guidance on product selection, installation, and maintenance, ensuring that customers get the most value out of their investment in Refractory Ceramic Fiber Blanket.Furthermore, the company's commitment to environmental sustainability is reflected in its manufacturing processes and product development. Refractory Ceramic Fiber Blanket is designed to have minimal environmental impact, making it a responsible choice for businesses looking to reduce their carbon footprint and comply with stringent environmental regulations.The announcement of the factory price for Refractory Ceramic Fiber Blanket is a clear demonstration of the company's dedication to meeting the evolving needs of its customers and the industry as a whole. As demand for high-performance insulation materials continues to rise, {} is poised to be a trusted partner for businesses seeking reliable and cost-effective solutions.With a strong emphasis on quality, innovation, and customer satisfaction, {} is well-positioned to continue leading the way in the refractory products industry. The announcement of the factory price for Refractory Ceramic Fiber Blanket is just the latest example of the company's commitment to delivering value and driving positive change in the industrial sector.